Welding of nitrided structural steel
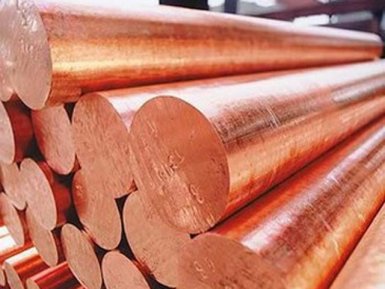
Are you interested in welding nitrided structural steels from the supplier AvecGlob? Here you will find interesting information on this topic.
General issues of weldability of nitrided steels
Nitrided steels — doped, or with nitride-forming components in the composition — are predominantly low-carbon. Nitriding helps to increase their surface hardness. Such steels are used in applications where it is necessary to significantly increase the wear resistance of the surface.
Formally, a small percentage of carbon should contribute to good weldability. In fact, everything goes wrong, because the high hardness of the surface layers and increased heat resistance leads to the fact that welding of such steels requires highly concentrated processes, including electron beam and plasma arc welding.
Plasma welding or plasma nitriding?
Plasma arc welding is used more often. It’s not just that it is more affordable in terms of its total costs. Plasma, being a highly concentrated heat source, allows to prolong the process of saturation of the surface layers of the connected parts with nitrides, especially if the plasma is supported in a gas nitrogen containing medium. Incidentally speaking, plasma welding, along with the actual joining, further nitrides the surface.
Plasma nitriding significantly increases the surface hardness (due to which the joint site is often subjected to annealing), provides increased nitriding productivity, allows to regulate the amount of nitrides and ensures a smoother transition from the nitrided layer to the base metal structure.
Supplier — AvekGlob company — offers at a reasonable price from the manufacturer a diverse assortment of nitrided structural steels that meet the technical requirements of domestic and foreign standards. The supplier guarantees the timely delivery of products to any address specified by the consumer.
Kinetics of nitride formation in welding
This process is based on the formation of solid compounds on the surface of steel. Elements capable of forming nitrides should be present in the steel as alloying elements. They include Al, Ti, Cr, Mo, W and V. Nitriding is particularly suitable for tool steels that contain many of these alloying elements.
The formation of nitrides gives a very hard surface, with a hardness of up to 1500HV, with good resistance to fatigue due to the presence of compressive stresses. Unlike cemented layers, this hardness can be maintained at temperatures up to 500 ° C. Plasma nitriding is a similar process for plasma carburizing, but using a nitrogen-hydrogen gas mixture, rather than a hydrocarbon for producing plasma by the glow discharge method. Furthermore, no separate heating is required, since the plasma provides sufficient heating of the surface of the component to achieve the process temperature, typically 500 ° C.
When welding with a plasma arc, carbon no longer contributes to hardening, as: surface hardness increases due to the formation of nitrides (for the alloyed structural steels the process is more efficient). As a consequence, the final stage of quenching of nitrided steels welded in this way is not required.
Supplier — AvekGlob Company — offers to purchase various grades of structural nitrided steels that meet all technical standards and requirements. Products can be bought at a price formed on the basis of European and world standards of production. Implementation is possible in bulk and retail, for regular customers, a flexible system of discounts operates.