Low alloy structural steel for welded structures. History and interesting
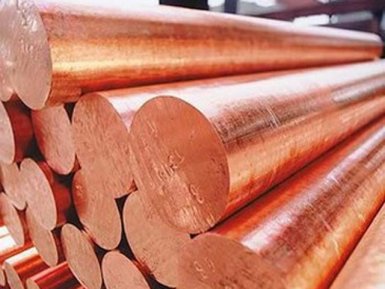
Are you interested in low-alloy structural steels for welded structures from the supplier AvecGlob? Here you will find interesting information on this topic.
General information
The development and use of high-strength low-alloy steels for welded structures is caused by the need to reduce costs, higher strength compared to conventional carbon manganese steel, which allows the installation of thinner and lighter structures. Most of these steels are used for the manufacture of offshore structures, buildings, ships, etc. The tensile strengths of up to 690 MPa are achievable, with good weldability and high toughness, often exceeding 50 J, even at negative temperatures (down to -60 ° C).
Production
There are two methods by which high tensile strength and toughness are achieved — by microalloying, adding small amounts of strong carbide and nitride-forming components and very careful monitoring of rolling or thermomechanical processing of steels. The greatest advantages are achieved by a combination of two methods. The goal is to have the structure as fine-grained as possible: a fine grain, provides the best impact strength and an increase in tensile strength (up to 50%).
Improved weldability is an additional goal, it is achieved by reducing the hardenability of steel containing less than 0.05% carbon and reducing the sulfur and phosphorus content.
Features of chemical composition
To compensate for the loss of carbon and increase the tensile strength, small additions of alloying elements-niobium (<0.10%), titanium (<0.030%) and vanadium (<0.15%), sometimes also add molybdenum, chromium, copper and nitrogen. These elements refer to carbide and nitride-forming, inhibit grain growth during hot rolling and help in the nucleation of fine-grained ferrite during cooling. These elements also provide some increase in strength by quenching.
Supplier — AvekGlob Company — offers at a reasonable price from the manufacturer a diverse range of low alloy structural steels for welded structures that meet the technical requirements of domestic and foreign standards. The supplier guarantees the timely delivery of products to any address specified by the consumer.
Rolling
Controllable rolling can also be used to provide additional grain refinement and, consequently, increased tensile strength and viscosity increase. Rolling of such steels is carried out at a temperature near or slightly below the recrystallization temperature of steel, i. E. not higher than 900 ° C, which leads to the formation of elongated austenite crystals.
Accelerated cooling from the rolling temperature leads to the formation of a very fine-grained ferrite at the boundaries of the austenite grain.
Welding modes
Steels intended for the manufacture of welded structures can be welded with lower preheating temperatures than is customary for conventional carbon-manganese steels. Thus, the metal of the welded joint has the greatest risk of cold cracking in these types of steels. There are several reasons for this;
The high strength of the base metal means higher residual stresses during welding;
To match the tensile strength and toughness of the original steel, fillers must be highly alloyed;
The weld metal is converted from austenite to ferrite at a lower temperature than the original steel.
Supplier — AvekGlob company — offers to purchase various grades of low alloy structural steels for welded structures that meet all technical standards and requirements. Products can be bought at a price formed on the basis of European and world standards of production. Implementation is possible in bulk and retail, for regular customers, a flexible system of discounts operates.