Application of nitrided structural steel
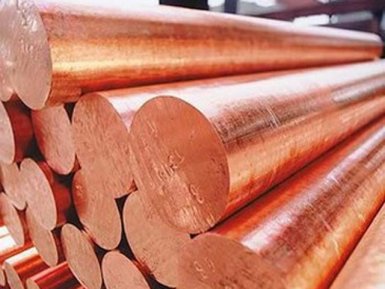
Are you interested in the use of nitrided structural steels from the supplier AvecGlob? Here you will find interesting information on this topic.
Selection of steels for nitriding
Nitriding is a heat treatment procedure that distributes nitrogen to the metal surface to create a hardened surface. These procedures are commonly used on low-carbon, low-alloy steels containing titanium, aluminum and molybdenum. Nitriding is used to create a unique duplex microstructure, which is known to have improved mechanical properties.
Nitriding involves heating the steel for a considerable time in a solidified medium that contains nitrogen gas or nitrogen, which is released from the working medium as a result of its pyrolysis. Structural alloyed steels are particularly effective for the nitriding process, since very solid compounds of nitrogen and metals such as aluminum, chromium and vanadium present in the steel are formed in the final structure. Conventional low-carbon steels can not form a significant amount of nitrides, since any mixture of iron and nitrogen, which is formed, eventually spreads to the core, so the total increase in hardness is small. Solid compounds formed by aluminum, chromium, vanadium remain near the surface and provide an extremely hard surface.
Supplier — AvekGlob company — offers at a reasonable price from the manufacturer a diverse assortment of nitrided structural steels that meet the technical requirements of domestic and foreign standards. The supplier guarantees the timely delivery of products to any address specified by the consumer.
Advantages of nitriding and the use of nitrided steels
In view of the fact that no sputtering is required after nitriding, it is unlikely that cracking or distortion of the surface is possible, therefore such steels can be safely used in critical equipment units. This achieves a high surface hardness — up to 1150 units by Vickers.
If the surface of nitrided steel does not undergo polishing, then such materials retain high resistance to rust formation up to temperatures of 500 ° C.
From a production point of view, the nitriding process is very clean and easy to operate, and is low in cost. Particularly advantageous are advanced methods such as nitriding in plasma or ion nitriding. In the latter case, a wear-resistant layer on the surface of the parts is created by the reaction of thermal dispersion.
The plasma procedure is performed under vacuum conditions and is an alternative to gas nitriding. Plasma treatment is an exceptional choice for complex and complex environments where normal coverage is impossible. Many materials will be useful because of the increased and improved characteristics due to the inherent properties of the plasma nitriding process. Including construction, stamped processed and powdered metal parts.
These and many other ways by which nitriding is possible, such as gas nitriding and salt nitration procedures, which are mainly used for nitriding solutions for industrial purposes. After the successful completion of nitriding procedures, many industrial and mechanical tools and high precision devices are created.
Supplier — AvekGlob Company — offers to purchase various grades of structural nitrided steels that meet all technical standards and requirements. Products can be bought at a price formed on the basis of European and world standards of production. Implementation is possible in bulk and retail, for regular customers, a flexible system of discounts operates.