Magnesium European brands
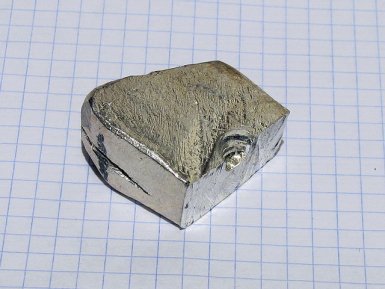
General characteristics
Magnesium is an exceptionally lightweight, silvery-white metal of the periodic table of the chemical. elements, number 12, denoted by Mg. Under normal conditions the air is almost constant from oxidation protects the surface of thin oxide layer. Magnesium has a boiling point equal to 1103 °C, its density is about 1.7 g/cm3 at 20 °C and the melting point of magnesium is 650 °C. the surface of the magnesium is covered with the oxide film, which collapses at a temperature of 623 °C, after which it burns. Magnesium powder and the foil is ignited with ordinary matches and burn in air and carbon dioxide.
Physical properties | |
---|---|
Atomic (molar) mass, g/mol | 24,3 |
Oxidation | 2 |
Density [g/cm3] | 1,738 |
The melting temperature t°C | 650°C |
The heat of fusion kJ/mol | 9,2 |
The thermal conductivity K [W/(m·K)] | 158 |
Heat of evaporation kJ/mol | 131,8 |
Magnesium is one of the most high-tech metals: it is well pressed, bent, easily drilled, cut and rolled. But pure magnesium is rather fragile, therefore, as a structural material alloys are more valuable. With a large number of metals, magnesium is able to form materials resistant to corrosion with high specific strength. Electrical resistivity of magnesium at a temperature of 20 °C is 0,047 Ohm • mm2/m.
Technological properties of Mg | In wrought form | In the ingot |
---|---|---|
Yield strength | 88 MPa | 30 MPa |
Temporary resistance of the load | 196 MPa | 118 MPa |
Hardness | 36 HB | 30 NV |
The modulus of elasticity E | 41000−43000 MPa | 42000−44000 MPa |
Elongation | 12% | 8% |
Casting
The magnesium melting temperature almost 30 °C greater than the ignition temperature of its air, which greatly complicates the melting of alloys of magnesium and of the metal itself. Magnesium dust ignited even at a lower temperature therefore before the heat treatment, the metal must be cleaned from shavings, burrs and dust.
Magnesium ingots according to the standards GOST 804−93 cast of four stamps, three of which — General purpose: the brand Mg80 comprises a pure Mg — 99,80% brand Mg90 contains 99,90%, Mg95 contains 99.95 percent, and the brand special purpose Mg98, comprises 99.98% of pure magnesium. The molten metal differs coarse structure and low strength. To achieve the maximum ductility of the magnesium alloys and the metal itself heated to a temperature of 320−430°C before pressure treatment.
Use
Magnesium in its pure form is quite rare: in the chemical industry, in pyrotechnics, metallurgy in the form of a reducing agent, alloying element and deoxidizer. Most often it is used in the manufacture of stronger and lighter alloys, which are in demand in the aerospace industry and the automotive industry.
Magnesium alloys
The most common alloys include alloys of magnesium and aluminum, zinc, manganese, lithium. As an additional alloying element used cadmium, cerium, zirconium, neodymium and other elements. Typically used in the automotive industry magnesium alloys with zinc, zirconium and aluminium, which are operated with a slight temperature. To increase the mechanical qualities of the alloy is achieved at elevated temperatures by adding neodymium, cerium, and thorium. Zirconium and cerium contribute to the modification of the structure of the material. Adding Zirconia in an amount of 0.5−0.7 percent lower to 100 times the grain size. Manganese and zirconium reduce the harmful effects of Nickel and iron on the properties of the alloys.
Heat treatment
In the heating process significantly increases the solubility of alloying elements, which gives the opportunity to strengthen the alloy by artificial aging and hardening. However, heat treatment of this type is complicated by the magnesium in solid solution due to the low rate of diffusion processes. This requires prolonged exposure at high temperatures (up to 30 hours) to dissolve the secondary phases. In this case, the alloy can be hardened by air cooling. Magnesium alloys have a tendency to natural ageing. Artificial aging requires) at 200 °C is also great endurance (up to 24 hours). Other types of heat treatment it is necessary to mention different types of annealing to remove residual stresses. To increase strength can also be a way of thermomechanical treatment, which consists in plastic deformation of the alloy in the hardened form before aging.
Advantages
Magnesium alloys are easy and, consequently, high specific stiffness and specific strength in terms of weight. These alloys can easily absorb vibration. In addition, they are high-tech: easily pressed, rolled, cut, drilled, soldered and welded.
Disadvantages
The disadvantages include the difficulties that arise in casting, melting and solidification of alloys. Given that magnesium is easily oxidized, the corrosion resistance of magnesium alloys is not very high.
Use
Magnesium alloys are very popular in the defense and aerospace industry, automotive industry and textile machinery in the manufacture of rotating parts with small inertia; in the manufacture of lightweight portable tools and appliances, etc.
Magnesium alloys and their percentage composition (according to GOST 2581−78):
Alloy doped MM2 to 1.5 — 2.2% manganese. Impurities of iron, silicon, aluminum, copper, Nickel ranges from 0.03 to 0.07%.
Alloy doped Mm2ch of 1.7 — 2.4% manganese. Impurities of iron, silicon, aluminum, copper, Nickel ranged from 0.01 to 0.06 percent.
MA8C alloy doped by 7.5 — 8.7% aluminum, 0.3 mm -0,8% zinc and 0.2 — 0.5% manganese. Impurities of iron, silicon, aluminum, copper, Nickel ranging from 0.02 to 0.1%.
Ma8cch alloy doped by 7.5 — 8.7% aluminum, 0.3 mm -0,8% zinc and 0.2 — 0.5% manganese. Impurities of iron, silicon, aluminum, copper, Nickel amount to from 0.05 to 0.01%.
Ma8cje alloy doped by 7.5 — 8.7% aluminum, about 0.3 to 1.5% zinc and 0.2 — 0.5% manganese. Impurities of iron, silicon, aluminum, copper, Nickel ranged from 0.01 to 0.05%.
Ma8cbch alloy doped by 7.5 — 8.7% aluminum, 0.3 mm -0,8% zinc and 0.2 — 0.5% manganese 0,001 — 0,002 Ve%. Impurities of iron, silicon, copper and Nickel (in descending order) from 0.05 to 0.01%.
Alloy MA10C1 doped 9 — 10% aluminum and 0.7 to 1.2% zinc and 0.2 — 0.5% manganese. Impurities of iron, silicon, aluminum, copper, Nickel ranged from 0.15 to 0.05 percent.
Alloy Mcr1n3 doped with 0.2 — 0.5% manganese and Zr of 0.4 — 1.1% and Nd of 2.6 to 3.2%. Impurities of iron, silicon, aluminum, copper, Nickel ranged from 0.04 to 0.01%.
These alloys are used in the production of magnesium structural alloys as sitovoj component.
Among the wrought and cast magnesium alloys distinguish alloys with special properties: ultra-light, protective, high damping capacity and high sound conductivity.
Buy at best price
A huge range of metal stock LLC «AVEK global» can satisfy any customer. Absolute compliance with all technological norms of production ensures the quality of the finished product. Deadlines all orders the shortest possible. For any questions, experienced managers will give a full detailed advice. Carrying out wholesale orders, you can count on company-provided flexible system of discounts.