Thread tungsten
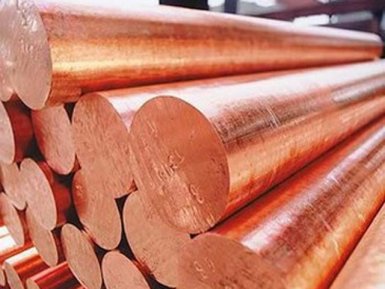
History
Manufacturing tungsten filament, injured as a failure, ended with the opening of a new direction — technology of powder metallurgy. We are all familiar incandescent bulbs appeared on the eve of 1905, and before that there was an active search for sources of light in light bulbs. The search lasted for more than 25 years until, in 1878, Swan first introduced invented carbon lamp, the brightness of which was eight — sixteen candles. By the end of the NINETEENTH century von welsbach was made of osmium (melting point 2700°C) metal filament. Osmium lamp was much brighter and more efficient coal, but the cost of osmium, which belongs to the platinum group elements, making them prohibitively expensive.
Von Bolton, an employee of the company «Halske and Siemens» for the filaments suggested Tantal with t° melting point of 2996° C. the tantalum Lamp was 15 percent more efficient osmium, they have already started to implement in production. However, a year later, a tungsten filament, tantalum — are unable to compete. Tungsten lamps are quickly pushed out of the market all other modifications. Their luminous efficiency was two to four times higher than that of osmium. Modern fluorescent lamps with W-cathode almost an order of magnitude brighter and more efficient osmium late nineteenth century.
The development of the technology
The main difficulty was the lack of ductility of tungsten. It is not possible to successfully carry out the drawing process of tungsten filament with the help of technology developed for tantalum. Later on «Siemens Halske» it was decided to use an electric arc in a hydrogen atmosphere to obtain a molten tungsten, which later received the processing.
Also, I tried mixing organic components with tungsten powder, and the thus obtained paste, began to pass through the die and burned in the special atmosphere of the binder component for the purpose of receiving the thin fibers without impurities. Even tried to heat the coal thin filament in the atmosphere vapour testiclesthe WCL6 and hydrogen. Tungsten, deposited on the surface was caked with carbon, forming the carbide WC — fragile thread of white color. After that, the filament was heated, the flow of hydrogen «washed» carbon, leaving a thread of pure tungsten.
The main complexity of the technology was rapid oxidation of tungsten at high temperatures with the formation of fragile grainy structures. However, already at the end of the first decade of the twentieth century Coolidge from the USA was able to choose the most optimal mode of mechanical t heat treatment, thereby obtaining ductile tungsten without the use of fillers.
Modern production methods
The tungsten powder should have a high purity for high-quality production. Using special mills under the protection of nitrogen atmosphere (to be heated by friction of the metal is not oxidized) are mixed powders of tungsten of different origin. With a steel mold powder is compressed under a pressure of 5−25 kg/mm2. When contamination of the powder pressing out fragile. To reduce brittleness, is added easily oxidizable organic component. Heating in a stream of hydrogen increases the mechanical characteristics of pressovac. Further rods at very high temperature sintered. When heated nearly to the melting point — increasing grain size, the material is sintered to 95% density of crystalline tungsten. Further rashkovka occurs at a temperature of 1200−1500°C.
Hammer rods are compressed under a pressure of 500 to 2500 ATM., each time they become 12% thinner. The elongation of the grains is achieved by a fibrillar structure. Thread after forging is pulled through the sieve of WC carbide or diamond. The diameter of the filament obtained by this method is порядка13 microns.
Advantages
Tungsten filament made of the refractory metal, t° melting +3422°C, it has not only high heat resistance but also corrosion resistance to aggressive environments, which allows her to apply for the most important products. It has excellent mechanical properties: abrasion resistance, minimal thermal expansion coefficient, hardness at high temperatures compared to other metals, high modulus of compression-tensile, very high electrical resistivity, creep resistance, good thermal conductivity. The durability and reliability of the tungsten filament in the most extreme conditions made it irreplaceable in modern industry.
Physical quality | |
---|---|
The temperature at which the obtained data the features of t°C | 20°C |
The linear thermal expansion coefficient α [1/Deg] | 43x10-6 |
The density of the alloy [g/cm3] | 19,3 |
Tensile strength tensile kg/mm2 | 35 |
Specific heat at 20 °C [kJ/(kg·deg)] | 0,134 |
The thermal conductivity K [W/(m·K)] | 300,173 |
Electrical resistivity R, Mhmm2/m | 0,054 |
Disadvantages
Tungsten is a rare element in the earth’s lithosphere. At ordinary temperatures it is not ductile. The difficulty of obtaining it in its pure form, rather complicated processing due to its unique properties affects the cost of the final product.
Use
High resistivity, as well as the unique light output allow you to use tungsten lighting. Regulates the production of stamps VA, VRN, RF diameter from 19.5 microns up to 1.5 mm GOST 19671−91. Serve as the basis of springs of semiconductor and electronic devices, the helical cathodes for electronic devices and respiratoorse loop cathodes, grids, and heaters. Also used in rocket and aircraft construction, textile industry, mechanical engineering. Filters made from tungsten wire is widely used industrial chemicals.
Buy at best price
A large range of high quality tungsten filament with different diameters of stock LLC «AVEK global» can satisfy any consumer. The quality of the finished product is ensured absolute compliance with all technological norms of production. The order execution time is the shortest. If you have any questions, you will receive detailed advice from experienced managers. For wholesale orders the company provides flexible system of discounts.