Cementable structural steel. History and interesting.
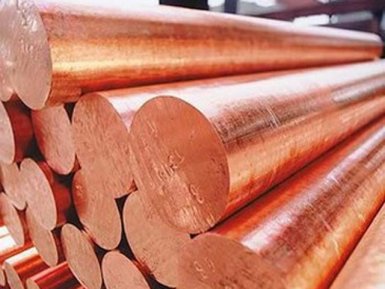
Are you interested in the characteristics and history of cemented steels from the supplier company AvecGlob? Here you will find interesting information on this topic.
History
Cementation is used for a long time. Nevertheless, the carburizing process was sufficiently developed only with advances in heat treatment methods that improved the hardness and durability of products such as springs or forgings made of carbon steel.
Hardening of the surface of the part is achieved due to carbon saturation of the surface layer, which receives increased fatigue strength and wear resistance. The effectiveness of carburization is largely dependent on the carbon content of the steel. When the carbon content in the steel exceeds a certain percentage, the further addition of carbon to hardness does not affect — the additional carbon at this stage does not dissolve.
When the carburization time is extended to obtain an increased depth of the housing, excess free carbides can form. Microstructural elements have an adverse effect on the distribution of residual stresses.
Carbon steels typically have a carbon base content of about 0.2%, while the carburized layer has a carbon content of between 0.8% and 1%. Most cemented steels are deoxidized by the addition of aluminum. Due to differences in the carbon content in the core and the casing, their ability to increase the hardness is also different.
Where applicable
Cementation is effective for gears, dies and responsible mechanisms. As a result of carburization, a solid, carbon-rich layer is formed on the outer surface of the heat-treated components, while the core of the billet remains relatively ductile.
All cycles for carburizing heat treatment of parts and forgings are carried out in specialized furnaces of periodic heating. These furnaces allow for optimal control of the process.
The process of heat treatment by carburizing
The process of heat treatment of carburizing for machined parts and stamping begins with austenization of heat-insulating materials. Further, the workpieces are loaded in a furnace with a controlled, carbon-rich atmosphere. Duration of exposure is determined by the requirements for the depth and hardness of the cemented layer.
Then the parts are hardened. Selective hardening of the cemented surface is possible due to the application of kraft-stop paints.
To obtain already processed parts with wear-resistant surfaces, thermal treatment by carburizing is also used. For the decomposition of residual austenite quenching, especially for high-alloy steels, after the cementation, cold treatment is performed.
Supplier — AvekGlob Company — offers at a reasonable price from the manufacturer a diverse assortment of cemented structural steels that meet the technical requirements of domestic and foreign standards. The supplier guarantees the timely delivery of products to any address specified by the consumer.
Process Benefits
Cementation is advisable to be used for high-performance mechanical gears and bearings, for transport units, as well as for new applications with increased depth of the cemented layer, which include heavy-duty materials for punching and forging steel.
As a result, a new class of steels is created with special emphasis on new applications with a hard surface, resulting in increased wear resistance and durability.
Supplier — AvekGlob Company — offers to purchase various grades of constructional cemented steels that meet all technical standards and requirements. Products can be bought at a price formed on the basis of European and world standards of production. Implementation is possible in bulk and retail, for regular customers, a flexible system of discounts operates.