Welding of cemented structural steel
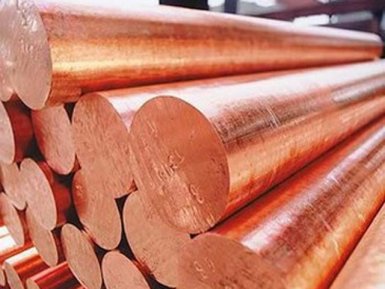
Are you interested in welding cemented steels from the supplier AvecGlob? Here you will find interesting information on this topic.
Problems in welding cemented steels
When welding cemented structural steels, they should be preheated from 150 to 260 ° C, depending on the carbon content and the thickness of the steel. During welding, the welding zone will be quenched with rapid cooling and after welding, internal stresses must be removed. Steels subjected to carburization can be welded by any processes of arc welding, gas welding, and resistance welding. At a higher percentage of carbon and manganese, electrodes with a low hydrogen content should be used. Electrodes made of low-carbon steels are also used, which work well on any polarity of the welding current. Minor parts should be annealed to reduce the hardness before welding.
The parts must be preheated at the joint, and after welding the whole weld zone should be heat treated to restore the original properties of the materials.
For welding medium carbon steels, a low-carbon or high-strength welding electrode can be used. The welding flame must be adjusted so that the metal melt zone is minimally permissible. Welding with a carburizing flame causes the metal to heat up quickly, because heat is released, when the steel absorbs carbon. This allows you to drive the process at higher speeds.
Care must be taken to slowly cool the parts after welding, otherwise it may crack the weld.
Supplier — AvekGlob Company — offers at a reasonable price from the manufacturer a diverse assortment of cemented structural steels that meet the technical requirements of domestic and foreign standards. The supplier guarantees the timely delivery of products to any address specified by the consumer.
Features of welding technology
The entire joint area must be tempered by heating to 590… 680 ° C, and then cooled slowly. Cooling can be performed by coating the parts with refractory material or sand. Mild steel is better welded by the metal arc method with shielded arc electrodes made of mild steel.
During this process, the metal heats up, and then melts, turning into a liquid state. On the surface remain slags and fusible inclusions.
Typically, in all electric arc processes, the weld zone is shielded by shielded gases to avoid oxidation occurring in the weld pool. All processes differ depending on the amount of heat released, the rate of heat supply and the concentration of heat.
Common factors that can change for changing deposition rate and penetration range are given below:
Melting of the welding electrode
Melting of base metal
Heat distribution in a metal plate
As a result of properly performed welding, the metallurgical changes that occur during the process will be the same for all welding methods.
The formation of heat varies from process to process, where the oxygen-containing welding process generates more heat on the surface and melts less, and in the arc welding process, the melting is greater and the heating of the metal is less.
Supplier — AvekGlob Company — offers to purchase various grades of constructional cemented steels that meet all technical standards and requirements. Products can be bought at a price formed on the basis of European and world standards of production. Implementation is possible in bulk and retail, for regular customers, a flexible system of discounts operates.