Welding of nickel alloys
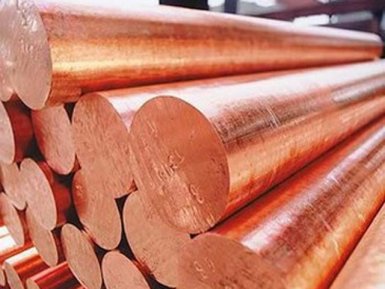
Are you interested in welding nickel alloys from the supplier company AvecGlob? Here you will find interesting information on this topic /
General issues
Nickel alloys can be reliably connected by all types of welding processes or methods, except for forge welding and oxyacetylene welding. Forged nickel alloys can be welded under conditions similar to those used for welding austenitic stainless steels. The greatest difficulties arise when welding cast nickel alloys, especially with a high content of silicon.
Welding methods
The most widely used methods of welding nickel alloys are gas-tungsten arc welding, gas welding (GMAW) and shielded arc welding.
Welding under the flux layer, electroslag and plasma welding are of limited applicability.
Preparation
Nickel alloys are usually welded by careful preparation of the surface (degreasing, annealing and other operations that relieve internal stresses and reduce the risk of stress corrosion cracking). To restore corrosion resistance, no treatment after thermal or chemical treatment is required.
Surface cleaning is necessary, since nickel alloys are susceptible to embrittlement by lead, sulfur, phosphorus and other elements with a low melting point. These materials can exist in grease, oils, paints, etc. For mechanical cleaning, grinding, abrasive blasting or etching in hydrochloric acid solution is used. From the weld area, oxides must be removed (mainly because of the difference in the melting points of the oxide and base metal).
Supplier — AvekGlob Company — offers at a reasonable price from the manufacturer a diverse range of welded structures made of nickel-based alloys. The supplier guarantees the timely delivery of products to any address specified by the consumer.
Recommendations for the welding of nickel alloys
For manual and machine welding, reverse polarity of direct current is used. As protective gas for welding nickel alloys, either argon or helium or a mixture thereof is used. The presence of oxygen, carbon dioxide or nitrogen usually causes porosity or erosion of the electrode. This can be avoided if argon is used with small amounts of hydrogen (usually up to 5%); while the amount of oxides formed on the surface is also reduced.
Features of the technology of welding of nickel alloys
Any part subjected to strong bending, stretching or other molding operations, must be annealed before welding. If possible, heating should be carried out in a controlled atmosphere oven to limit oxidation and minimize subsequent surface cleaning.
The heat balance during welding should be maintained at a moderately low level in order to obtain the maximum possible connection efficiency. For multilayered welds, a lot of narrow edges should be used, rather than several large heavy ones.
To achieve optimal results when welding cast nickel alloys, casting must be pre-annealed. Preliminary gripping of the metal after the first pass removes stresses and, thus, reduces cracking at the joint. After the end of welding, it is necessary to remove residual stresses, using postoperative annealing.
Supplier — AvekGlob Company — offers to purchase various welded constructions made of nickel alloys. Products can be bought at a price formed on the basis of European and world standards of production. Implementation is possible in bulk and retail, for regular customers, a flexible system of discounts operates.