Manufacture of nickel alloys
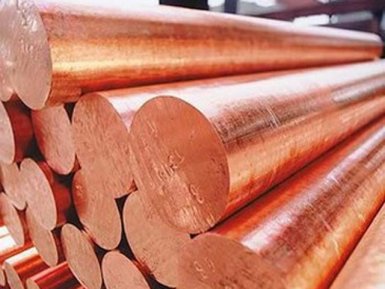
Are you interested in the production of nickel alloys from the supplier company AvecGlob? Here you will find interesting information on this topic
Production technology
About 80 percent of the production of nickel and its alloys comes from sulphide copper-nickel ores. Selective ore concentration by flotation gives concentrates of copper, nickel and pyrrhotite.
The nickel ore concentrate melts in the presence of fluxes in electric or reverberation furnaces to separate the waste rock and to extract nickel in the form of a sulphidic melt (matte), which contains 10−15 percent nickel. Electric smelting (the main method of nickel smelting in Russia) is usually preceded by partial oxidizing firing and fragmentation of the concentrate into fragments. In addition to nickel, some of the iron and cobalt, as well as virtually all copper and noble metals, go into slag. Separation of iron by oxidation (blowing liquid matte in converters) gives a melt of copper and nickel (nickel matte) sulphides, which is slowly cooled, finely ground, and sent to flotation to separate copper and nickel. The nickel concentrate is heated in a fluidized bed to produce nickel oxide. The metal is produced by reduction of nickel oxide in electric arc furnaces. The crude nickel is cast into the anodes and purified by an electrolytic method. The content of impurities in electrolytic nickel is 0.01%.
Supplier — AvekGlob Company — offers at a reasonable price from the manufacturer a diverse range of nickel-based alloys. The supplier guarantees the timely delivery of products to any address specified by the consumer.
Alternative technologies
The separation of copper and nickel is also carried out by the carbonyl process. The production of nickel carbonyl is carried out at a pressure of 100−200 at and at a temperature of 200−250 ° C, and its decomposition is carried out in the absence of air at a temperature of about 200 ° C at atmospheric pressure. This method is used in the production of nickel coatings.
In modern «autogenous» processes, melting is produced by heat released during the oxidation of sulfides by oxygen-containing air. This process eliminates carbon-containing fuel that is rich in SO 2, while sulfur oxide is used to produce sulfuric acid, which drastically reduces the cost of production. The highest efficiency and the greatest prospects are offered by oxidation of molten sulfides.
More widely accepted processes are based on the processing of nickel concentrates with solutions of acids or ammonia in the presence of oxygen at high temperatures and pressures (autoclave processes).
Nickel is usually dissolved and separated from the solution in the form of a rich sulphide concentrate or metal powder (reduction by hydrogen under pressure).
Nickel from silicate (oxidized) ores can also be concentrated in the form of matte by introducing fluxes (gypsum or pyrite) into the charge.
Reduction sulphurization melting is usually carried out in shaft furnaces. The resulting matte contains 16−20 percent Ni, 16−18 percent S, and the remainder Fe. The technology of extraction of nickel from the mat is similar to that described above, except that separation of copper separation often occurs.
The most expedient form of processing oxidized ores with a low cobalt content is the smelting reduction to produce ferronickel, which is used in the production of steel. To extract nickel from oxidized ores, hydrometallurgical methods are also used, such as ammonia leaching of pre-treated ore and leaching of the sulfuric acid autoclave.
Supplier — AvekGlob Company — offers to purchase various brands of nickel alloys. Products can be bought at a price formed on the basis of European and world standards of production. Implementation is possible in bulk and retail, for regular customers, a flexible system of discounts operates.