Methods of production of brass
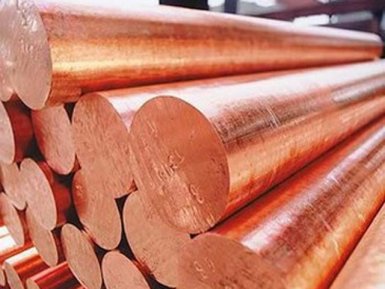
Are you interested in the processes of production of brass from the supplier company AvecGlob? Here you will find the necessary information on this topic.
Brass and its influence on the way of production
Brasses containing a high percentage of copper are produced from refined copper, which is at least 99.3%, in order to minimize the amount of other materials. Brasses containing a lower percentage of copper are more often made from brass scrap. When recycled scrap is used, the percentages of copper and other materials in it must be known so that the manufacturer can adjust the amount of materials added to achieve the desired brass composition.
The second component of brass is zinc. The amount of zinc varies from 5 to 40% by weight, depending on the type of brass. To improve machinability in brass, up to 3.8% lead is added, and tin is introduced into the alloy to improve corrosion resistance. Adding
iron makes brass more solid, and reduces the internal structure of the grain, which improves the plastic deformability of brass. Sometimes brass containing more than 20% zinc, arsenic and antimony are added to inhibit corrosion. Other materials that can be used in very small quantities are manganese, silicon and phosphorus.
Production process
The manufacturing process used to produce brass involves combining the respective starting materials in a molten metal that allows solidification. The shape and properties of the solidified metal are then varied through a series of carefully controlled operations to produce the desired brass material.
Brass blanks are available in various forms, including a plate, sheet, strip, foil, rod, rod, wire and forgings. Pipe rolling is formed by extruding, or crimping rectangular blanks of hot brass in dies.
Supplier — AvekGlob Company — offers various types of products from brass alloys of domestic and foreign production, which meets the requirements of standards. The products are offered at affordable prices from the manufacturer. The supplier guarantees the timely delivery of products to any address specified by the consumer.
Sequence of operations
Melting
The corresponding amount of scrap is weighed and transferred to an electric furnace where it melts at a temperature of about 1050 ° C. After the copper is melted, an appropriate amount of zinc is added (taking into account evaporation during melting).
If any other materials are required for a particular brand of brass, they are also added if they are not present in copper scrap.
The molten metal is poured into molds and left to solidify. In some variants of brass production, melting and pouring are carried out semi-continuously. Upon readiness, the preforms are unloaded from the molds and moved to the rolling zone,
Hot rolling
The blanks are placed in an oven and reheated to the desired temperature. Further, the blanks are fed through a series of rolling rolls, which gradually reduce the thickness of the brass. The ends of finished brass rolled are cut off on a milling machine. At the same time, from the external surfaces of the brass, any oxides that can be formed on the surface
Annealing and cold rolling
During the rolling process, the brass loses plasticity, so for the further deformation, it must first be heated to make the alloy more ductile. This process is called annealing. The atmosphere inside the annealing furnace is filled with a neutral gas, similar to nitrogen, to prevent the formation of unwanted oxides on its surface.
Then, cold rolling is performed to obtain the desired dimensional accuracy and surface quality assurance. Cold rolling deforms the internal structure of brass and increases its strength and hardness.
Supplier — AvekGlob Company — offers to purchase assorted brass alloys of domestic and foreign production. Products can be bought at a price formed on the basis of European and world standards. Implementation is possible in bulk and retail, for regular customers, a flexible system of discounts operates.