Manufacture of brass wheel, rod
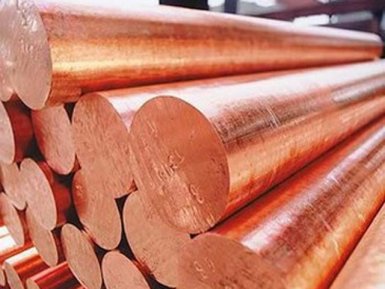
Are you interested in the production of brass rods and wheels from the supplier company AvecGlob? Here you will find the necessary information on this topic.
General issues of production technology
The brass bar and circle, which are made of high-grade brass grades, are usually manufactured using an integrated technology that includes transitions of plastic deformation of the initial blanks, their calibration, cleaning and quality control.
As equipment, hydraulic presses are used to extrude the material. Generally, indirect heating heaters are also built in the integrated production line, by means of which the initial preforms are heated. Hot extrusion reduces the strength of the process and increases the ductility of the starting material.
Rolled brass is widely used for the production of various fasteners, for the manufacture of valves used in various equipment, electrical parts, as well as in auxiliary components for automobiles and industrial equipment.
Bars and a circle of highly-brass brass are produced by the method of continuous vertical casting, after which, without additional heating, the brass semi-finished products enter the pressing line. For profiles of a small cross-section, technological processes of semi-hot or cold extrusion are used.
The quality control of the final product is carried out using non-destructive testing facilities, of which eddy current testing is most often used. The electromagnetic tester prevents the loss of the dimensions of brass blanks during their production.
Supplier — AvekGlob Company — offers various types of products from brass alloys of domestic and foreign production, which meets the requirements of standards. The products are offered at affordable prices from the manufacturer. The supplier guarantees the timely delivery of products to any address specified by the consumer.
Casting of brass bars
It is produced on two-position injection molding machines. Quality control of the process and the rate of formation of the required cross-sectional dimensions of the rod / wheel are made using level sensors. The casting speed is usually kept constant, so the unit can operate in fully automatic mode.
Casting molds are made of alloys with high specific conductivity, and the movement of all parts of the injection molding machine is synchronized, which ensures dimensional accuracy. The finished rod when cooled from the mold is cooled by a stream of water.
To reduce the wear of moving parts of the injection molding machine, which work in constant contact with the heated metal, an effective water-graphite lubricant is used. The working mixture is sprayed on the inner surfaces of the mold in small quantities by means of a reliable pump system. Lubrication is also applied to the guides, which allows to maintain a constant conveyor speed and reduce wear.
Supplier — AvekGlob Company — offers to purchase assorted brass alloys of domestic and foreign production. Products can be bought at a price formed on the basis of European and world standards. Implementation is possible in bulk and retail, for regular customers, a flexible system of discounts operates.