Processing, rolling and deformation of brass
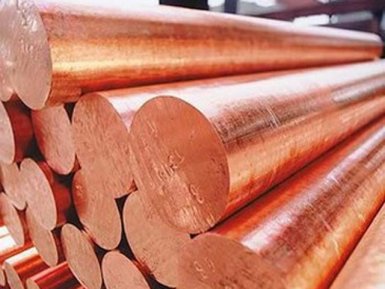
Are you interested in the technology of rolling and plastic deformation of brass from the supplier company AvecGlob? Here you will find the necessary information on this topic.
Rolling of brass alloys
Hot rolling
The blanks are placed in an oven and heated until they reach the desired temperature. The temperature depends on the final shape and properties of the brass material.
The heated preforms are then fed through a series of oppositely rolling rollers that gradually reduce the thickness of the brass to about 13 mm or less.
At the same time, the width of the brass increases. The brass that has cooled during rolling passes through a milling machine that cuts a thin layer from the outer surfaces of brass to remove any oxides that can form on the surface as a result of exposure to hot metal.
Annealing
As the brass is subjected to hot rolling, its plasticity gradually decreases, so for further deformation the alloy must first be heated to soften the metal. This process is called annealing. Temperatures and duration of annealing vary depending on the composition of brass and the desired properties. The rolled brass is placed in a sealed oven and annealed. Blanks with smaller dimensions can be placed on a metal belt conveyor and continuously fed through an oven with sealed seals at each end. In any of the methods, the atmosphere inside the furnace is filled with a neutral gas, for example nitrogen, to prevent the interaction of brass with oxygen and the formation of unwanted oxides on its surface.
Cold rolling
After annealing, the brass profiles are fed through another series of rolling rolls to further reduce the thickness to about 2.5 mm.
This process is called cold rolling, because the temperature of the brass is much lower than the hot rolling temperature. Cold rolling changes the internal structure of brass or grain and increases the strength and hardness of brass. The more the thickness decreases, the stronger the material becomes.
In the case of cold rolled sheets, wide sheets can be cut into narrower sections to produce a brass strip. The strips are then etched and washed.
Supplier — AvekGlob Company — offers to purchase assortment of various brass alloys of domestic and foreign production. Products can be bought at a price formed on the basis of European and world standards. Implementation is possible in bulk and retail, for regular customers, a flexible system of discounts operates.
Forging and stamping of brass and its alloys
Products made of brass and brass alloys undergo various forging and stamping operations, both cold and hot. Finished forgings are characterized by anisotropy of properties, high density, exact dimensions.
Formation under the influence of heat and pressure in accurate closed dies provides dimensional accuracy, excellent surface finish with a clean shiny appearance.
Advantages of forging and stamping of brass
High strength
When making forging, the metal is processed twice at enormous pressures: first during rod extrusion, and then during forging. This compacts the metal and produces the necessary grain or fiber structure.
Thus, the tensile strength of the parts increases, and the resistance to impact and abrasion increases.
Small tolerances
Forging in steel matrices ensures that the dimensions of the forgings correspond to the dimensions of the finished part, reduces, and in many cases eliminates the subsequent machining.
Performance
Forging and stamping of brass — very high-performance operations, which reduce the total cost of production.
Supplier — AvekGlob Company — offers various types of products from brass alloys of domestic and foreign production, which meets the requirements of standards. The products are offered at affordable prices from the manufacturer. The supplier guarantees the timely delivery of products to any address specified by the consumer.