Manufacture of brass pipes
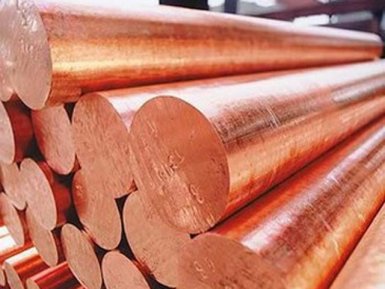
Are you interested in the production of brass pipes from the supplier company AvecGlob? Here you will find the necessary information on this topic.
Classification of brass pipes
Most brass pipes are produced by drawing or pressing technology. There are five ways to get pipes, choosing the right method or combination of methods for a particular application requires an understanding of the capabilities of each. Manufacturers of brass pipes also have a choice of raw materials: seamless or welded pipe.
Urgency of application
Brass pipes are used in such diverse applications as air hydraulic lines, diesel fuel lines, thermocouples, chromatography and semiconductor manufacturing. Tubular brass products for these applications often require careful size control, smooth and clean identification surfaces or other special properties. The correct pulling / drawing process can meet all these requirements.
Brass pipe drawing processes
The most commonly used tool for drawing is a matrix of sintered tungsten carbide, encased in a steel bandage. The cobalt content in the matrix material is about 10. A higher cobalt content provides greater impact resistance, while a lower content provides better wear resistance.
The main processes of drawing brass pipes are the sharpening, extrusion and piercing. When piercing the semifinished product is forced through the hole in the matrix, while the profile and configuration of the piercing provides the required wall thickness of the brass pipe. A free end for small diameter tubes is supported on the mandrel, while thick-walled brass pipes are deformed in a free state.
Brass pipes for consumer applications (production of furniture, sanitary devices, architectural compositions, etc.) are produced in several transitions, which are performed sequentially.
Supplier — AvekGlob Company — offers various types of products from brass alloys of domestic and foreign production, which meets the requirements of standards. The products are offered at affordable prices from the manufacturer. The supplier guarantees the timely delivery of products to any address specified by the consumer.
Elements of working equipment
The typical die angle is 24 0, and it has a relatively long bearing. Lower angles tend to cause wall thickening, whereas higher angles cause wall thinning. During the dipping, a long bearing is used to achieve the correct size and optimal roundness, which makes this process suitable for the final calibration operation.
In the drawing process of brass pipes, the billet is passed into a hardened steel rod or mandrel, which passes through the die using a special mechanism. Typical die angle is 36 0; bearing length is short. This process reduces the diameter of the pipe and the wall thickness.
For brass pipes of small diameter, an additional operation, called winding, is introduced. At the same time, the diameter of the tube is slightly increased so that the rod can be removed. The angle of the matrix affects the cleanliness of the surface of the tube — a small angle leads to a smooth finish, while an increase in the angle is accompanied by a deterioration in the quality of the brass tube. The length of the bearing must be long enough to provide the correct diameter and roundness, but not so much as to worsen the final surface.
Pipelines of ultrahigh pressure, as well as pipes of hydraulic pumps, made of brass, are usually calibrated during the winding of the rod.
Supplier — AvekGlob Company — offers to purchase assorted brass alloys of domestic and foreign production. Products can be bought at a price formed on the basis of European and world standards. Implementation is possible in bulk and retail, for regular customers, a flexible system of discounts operates.