Contact welding of brass
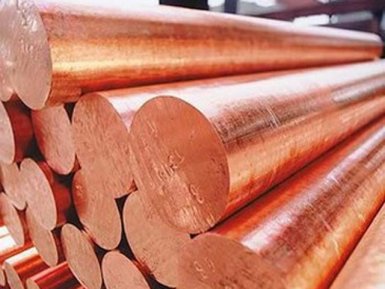
Are you interested in the technology of contact welding of brass alloys from the supplier company AvecGlob? Here you will find the necessary information on this topic.
Process Features
Contact welding or resistance welding is a thermoelectric process in which heat is generated at the junction of the parts to be connected by passing an electric current through the parts for a precisely controlled time and under controlled pressure (force). The name is due to the fact that the required value of the resistance of brass blanks or electrodes is used when they are tightly in contact with each other or contrasts with the formation of heat at the junction.
The quality of contact welding of brass products is affected by four key parameters — the brass alloy material, the energy, the applied connection force and the welding time.
The ability of brass alloys to contact welding
The physical metallurgy of materials to be welded determines the application of variable welding resistance. In general, there are two categories of metals that need to be welded: «conductive» (for example, aluminum, copper, silver and gold) and «resistive» (steel, nickel, inconel, titanium, tungsten, molybdenum). Brass belongs to the intermediate group.
Calculation of the required energy
To perform contact welding, energy is supplied by a welder using an internal or external transformer, which provides and controls the application of heat and time in the process of resistance welding. When welding brass alloys, higher current values are used at a relatively low voltage.
Supplier — AvekGlob Company — offers to purchase assortment of various brass alloys of domestic and foreign production. Products can be bought at a price formed on the basis of European and world standards. Implementation is possible in bulk and retail, for regular customers, a flexible system of discounts operates.
Control of welding modes
The sequence and modes of contact welding of brass are programmed by the technological equipment depending on the brass alloy fusion and the thickness of the products to be joined. Depending on the technical capabilities of the contact welding equipment, the user can program from one to more than 100 parameters and reset them during welding using the built-in microprocessor.
The range of modern welding machines for contact welding includes aggregates with an output of 5… 200 000 A, including a high-frequency inverter, a linear current converter, a capacitive unit and an alternating current pulse generator, which allows solving most problems with contact welding of brass alloys.
Clamping Force
The key parameter of all types of contact welding of brass alloys is the pressure that is applied to the weld. Correct and consistent application of the force improves the interfacing of brass products with each other, reduces the mechanical resistance at the junction and ensures the penetration of any oxide barriers between the blanks.
The regulator of repeated force ensures the repeated quality of welding of brass alloys due to the constant electrical contact resistance and a constant heat balance. Optimal welds are achieved when the applied force is accurate, repeatable, controlled according to a program, used to supply electricity and is regulated both to reduce the initial impact, and not to become excessive after contact welding.
Supplier — AvekGlob Company — offers various types of products from brass alloys of domestic and foreign production, which meets the requirements of standards. The products are offered at affordable prices from the manufacturer. The supplier guarantees the timely delivery of products to any address specified by the consumer.