Welding of brass electrode
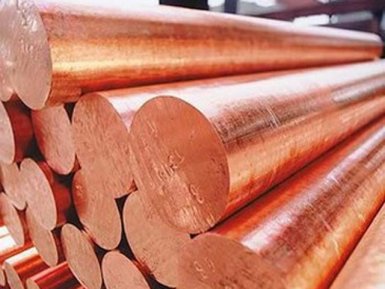
Are you interested in the technology of welding brass electrodes from the supplier company AvecGlob? Here you will find the necessary information on this topic.
Classification of electrodes used for welding brass
In international practice, there are three classes:
CLASS 1 — electrodes made of copper-zirconium alloys, which have a higher annealing temperature, 350 ° C, while maintaining comparable electrical and thermal conductivity. Recommended for welding brass alloys, especially with multi-layer coating (triple brass plates and plates);
CLASS 2 — Electrodes of chromium alloys with copper, the most widely used for spot welding electrodes of brass products. This material is a deposited material having a high annealing temperature of 500 ° C. It is recommended for welding brass with low electrical conductivity;
CLASS 3 — Copper and beryllium alloy electrodes with an optimum combination of viscosity, hardness and high annealing resistance at temperatures up to 550 ° C. It is recommended for welding special brass used for welding components that require high strength, wear resistance and good conductivity.
Supplier — AvekGlob Company — offers to purchase assortment of various brass alloys of domestic and foreign production. Products can be bought at a price formed on the basis of European and world standards. Implementation is possible in bulk and retail, for regular customers, a flexible system of discounts operates.
The use of tungsten non-consumable electrodes in the welding of brass
The process using such electrodes is called TIG, and it can be used to a limited extent in the manufacture of repair work with brass products. The rationale for the method lies in the fact that the installation of new brass parts is more expensive than surfacing / restoring the old ones.
Using tungsten electrodes for welding brass, the following should be considered:
In the process of welding TIG emits a lot of smoke, so an effective hood is needed, the Welder must work in a respirator, as zinc fumes are poisonous;
Welding is advisable to conduct on alternating current, using inverter welding units. The repetition rate of pulses should not exceed 30… 50 min -1 ;
Initially, the given amperage should be as high as possible to form a weld pool as quickly as possible. Only then a tungsten electrode is introduced into the welding zone;
It is inadmissible to overheat brass, resulting in zinc burnout;
It is advisable to use air cooling of the weld zone.
Supplier — AvekGlob Company — offers various types of products from brass alloys of domestic and foreign production, which meets the requirements of standards. The products are offered at affordable prices from the manufacturer. The supplier guarantees the timely delivery of products to any address specified by the consumer.