Welding in inert gases with a tungsten electrode
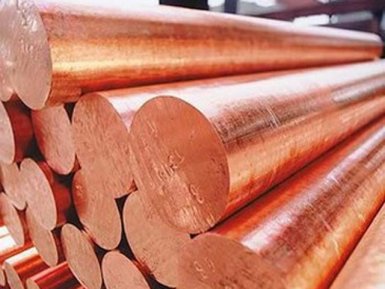
Are you interested in welding with tungsten non-consumable electrodes in the environment of inert gas from the supplier company AvecGlob? Here you will find interesting information on this topic /
General information about the process
Welding in an inert gas environment or gas-shielded arc welding is a popular technology for the non-removable connection of parts made of stainless steels and non-ferrous alloys, in particular nickel-based. The inert gas is used to protect the molten metal bath from the oxidizing effects of atmospheric air during welding. Shielding inert gases can be divided into two groups:
Gases that are soluble or reactive with metals. This is hydrogen, carbon dioxide, nitrogen, etc .;
Inert gases — helium and argon are most often used.
Of the above protective gases, practical application was obtained by argon, carbon dioxide, and — less — helium. Argon is produced as a by-product in the separation of air to produce oxygen. Gas is supplied in steel cylinders at a pressure of 150 atmospheres. Purified argon contains 97−98% of argon, but industrial argon is also used, which contains 13−14% nitrogen. To increase the welding efficiency, up to 5% of hydrogen is sometimes added to the inert gas.
Argon in the industrial state of purity is used for welding purposes. Argon with 5% hydrogen provides increased welding speed and penetration in the welding of stainless steel and nickel alloys.
Helium can be used for welding aluminum and its alloys, as well as copper and its alloys. But helium costs more than argon, and because of its lower density, more volume is required than argon to provide protection. A small change in the length of the arc leads to large changes in the welding conditions, so in practice a mixture of 30% helium and 70% argon is used. Such an inert gas composition in automated welding sets when welding aluminum provides increased depth of the weld and high speeds.
Supplier — AvekGlob Company — offers at affordable prices from the manufacturer tungsten non-consumable electrodes in the range, suitable for use in welding in an inert gas environment. The supplier guarantees the timely delivery of products to any address specified by the consumer.
The role of tungsten electrodes
Welding in an inert gas environment can use either non-consumable or consumable electrodes. In the version with a non-consumable electrode, the arc is supported between the tungsten electrode and the workpiece. The arc burns between the tungsten electrode and the blank inside the protective layer of the inert gas, which excludes oxygen from the atmosphere, and also prevents contamination of the electrode and molten metal.
A hot tungsten arc ionizes the argon atoms inside the screen to form a gas plasma consisting of an almost equal number of free electrons.
When hand welding in an inert gas environment, tungsten is not transferred to the workpiece.
In the aviation industry, arc welding in an inert gas environment is used on a large scale, despite its high cost. Before use, the inert gas should be dried by passing through a caustic or silica gel. The method of welding in inert gases with the use of tungsten electrodes is successfully used for welding of thin stainless steel, aluminum and its alloys, copper and its alloys, nickel and its alloys, titanium, zirconium, silver, etc. Tungsten arc with shielding from gas screens allows to weld these metals and a wide range of ferroalloys, which is an essential advantage of these processes.
Supplier — AvekGlob Company — offers to purchase tungsten non-consumable electrodes used in welding processes in inert gases. Products can be purchased at a price formed on the basis of European and world standards of production. Implementation is possible in bulk and retail, for regular customers, a flexible system of discounts operates.