Diameter and weight of tungsten electrodes
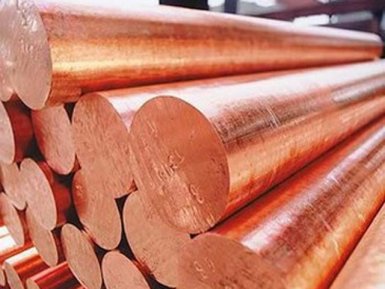
Are you interested in the weight and diameter of tungsten electrodes from the supplier company AvecGlob? Here you will find interesting information on this topic.
General information
The extensive use of mechanized and fully automated tungsten electrode welding technology has revealed the need for increased process productivity, in particular, increased arc stability, both for short-term and long-term processes. This is provided by using toric electrodes, which, however, have two significant drawbacks:
thorium is radioactive, and during repeated short-term ignitions, the arc actively evaporates from the surface;
electrodes wear out quickly.
The use of toric electrodes significantly increases the ventilation requirements of the rooms in which such welding is performed. Alternatives are tungsten electrodes with lanthanum or cerium present in the form of oxides of these metals. Argon is used as the protective gas.
Tungsten electrodes used in welding stainless steels are also selected for their dimensional characteristics — length and diameter. The choice is determined by the electric power of the process, the type of current (alternating or permanent), and its polarity.
Supplier — AvekGlob Company — offers tungsten non-consumable electrodes of various diameters and weights at a reasonable price from the manufacturer. The supplier guarantees the timely delivery of products to any address specified by the consumer.
Range of operating parameters influencing electrode size selection
The maximum idling voltage is not more than 80 volts;
The arc ignition time is no more than 35 milliseconds;
Welding current ranges: lower 5−75 amperes, upper 15−375 amperes;
Rated welding current: 300 A at 32 V, with a duty cycle of 60%.
Dimensions and weight of tungsten welding electrodes
The main thing is the correct choice of the diameter of the electrode, which depends on the calculated value of the current density. In this case, the length of tungsten electrodes is almost the same for all manufacturers, and is 175 mm, with an increase in diameter, the weight of the electrode increases.
For each welding condition, the optimum electrode diameter value is determined experimentally. If the end of the electrode melts, and the metal itself is not heated enough, then the stability of arc burning is disrupted. The minimum value of the density is determined by the intensity of erosion of the working end of the electrode. There is a minimum permissible current density below which the erosion of the electrode increases. The process is characterized by the gradual flow of tungsten to the end of the electrode, which substantially distorts its shape, and affects the accuracy of welding.
In practice, you can also use the tabular data:
Type of welding seam | The largest diameter of the electrode, mm | Welding current, A | The thickness of the metal workpiece, mm | Initial clearance between welded parts, mm |
1-sided | 3 | 180 | 3 | 1.9 |
2-sided | 4 | 220 | 5 | 1.5 |
2-sided | 5 | 260 | 7−8 | 1.5−2 |
2-sided | 6th | 330 | 10 | 2 |
This table is recommended for use with any welding mode:
Minimum thickness of welded metal, mm | 0.5 | 1−2 | 3 | 4−5 | 6−8 | 9−12 | 13−15 | 16 |
Thickness of tungsten electrode, mm | 1 | 1.5−2 | 3 | 3−4 | 4 | 4−5 | 5 | 6−8 |
Welding current, A | 10.20 | 30.45 | 65.100 | 100.160 | 120.200 | 150.200 | 160.250 | 200.350 |
Supplier — AvekGlob Company — offers to purchase tungsten non-consumable electrodes of various diameters, weights and composition. Products can be bought at a price formed on the basis of European and world standards of production. Implementation is possible in bulk and retail, for regular customers, a flexible system of discounts operates.