Spot Welding with Tungsten Electrode
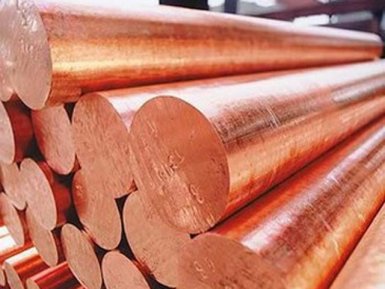
Are you interested in point welding using tungsten electrodes from the supplier company AvecGlob? Here you will find interesting information on this topic /
Process Features
Unlike conventional welding electrodes, whose properties and design cause them to conduct heat, electrodes made from refractory metals, in particular from tungsten, are chosen precisely because they retain heat well.
Tungsten is distinguished by the fact that it has the highest melting point (3387 ° C) among metals, and its hardness at any application temperatures is very high. As a rule, it resists oxidation, and its electrical resistance is very high. This feature of tungsten electrodes causes their use in the processes of spot welding of thin-sheet materials with low thermal conductivity (nickel and its alloys, copper and its alloys).
When choosing the size of a tungsten electrode for use in spot welding, it becomes important to control its inevitable oxidation during use and during welding. This allows the electrode to cool down as much as possible and faster. Tungsten is a very resistant metal from periodically occurring heat sinks, and this contributes to the high resistance of the electrodes.
A feature of tungsten, which should be taken into account in the development of spot welding technology, is that tungsten is produced from pre-sintered blanks of powder. Therefore, using electrodes not from chemically pure tungsten, but doped with less refractory metals (thorium, lanthanum, cerium, etc.), the possible dispersion of additives into the main element is as complete as possible.
Supplier — AvekGlob Company — offers tungsten electrodes at reasonable prices from the manufacturer, which can be used for spot welding of sheet blanks from various metals and alloys. The supplier guarantees the timely delivery of products to any address specified by the consumer.
Types of tungsten electrodes that are used in spot welding technologies
Electrodes made of tungsten alloys with copper or silver are available in different composition ratios, and are very widely used because they realize the optimum balance of copper and tungsten advantages. The silver / tungsten alloy is also produced with a different ratio of components, but is used primarily in soldering processes, since silver is difficult to alloy with iron and nickel. Tungsten-silver alloys are used for welding and soldering stainless steels and a number of nickel-based alloys.
Production technology
The above-mentioned doped electrode materials are the result of agglomeration hardening of the infiltration structure. A precisely measured bar of pure copper or silver is placed in a mold filled with an accurately measured amount of tungsten powder and baked in an oven with an inert atmosphere. The result is electrodes with high temperature and high electrical conductivity.
Other alloys with tungsten, which are used in spot welding
In specialized applications welding electrodes consisting of silver and tungsten carbide are used. This unusual electrode composition is chosen because tungsten carbide provides excellent oxidation resistance while maintaining its shape throughout the entire welding thermal cycle. Also known is a heavy tungsten alloy, which consists and consists of tungsten, iron, nickel and copper, which finds application in spot welding technologies.
Its advantages are excellent resistance to oxidation, as well as ease of processing compared to pure tungsten and tungsten carbide (WC).
Supplier — AvekGlob Company — offers to purchase tungsten non-consumable electrodes of various chemical composition and shapes, which are designed for spot welding. Products can be bought at a price formed on the basis of European and world standards of production. Implementation is possible in bulk and retail, for regular customers, a flexible system of discounts operates.