Preparation of metal for cutting
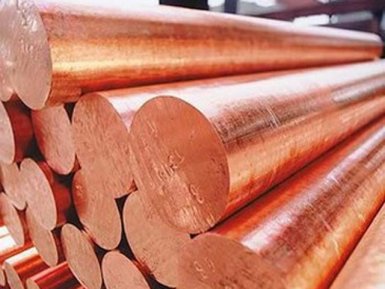
Are you interested in the technology of preparation for cutting of rolled metal, steels and alloys from the supplier company AvecGlob? Here you will find interesting information on this topic.
The essence of operations
For qualitative cutting of profiles and rolled metal, cleaning of the metal from scale is necessary, since the oxide film not only worsens the quality of the separation surface, but also contributes to the accelerated wear of the cutting tool. The exception is aluminum and stainless steels.
In order to improve the accuracy of cutting and improve the conditions for positioning long blanks — rods, wires, pipes — rolling is subject to correction.
To reduce friction between the tool and the workpiece, its surface is covered with special compounds, mainly phosphates and oxalic acid salts. Such operations are called phosphatation and oxalation, respectively.
Urgency of application
Cleaning of rolled products from process scale (especially for hot-rolled steel products) is typical for precision engineering, as well as for metalworking processes, which are produced in large scale and mass production plants. It is recommended to perform the correction for rolling and length gauges with small longitudinal stiffness. Phosphating and oxalation are carried out only before cutting the blanks by the method of plastic shearing.
Supplier — AvekGlob Company — offers at affordable prices from the manufacturer various metals and alloys, blanks for which can be obtained using various cutting processes. The assortment and the number of such blanks are completely determined by the customer’s wishes. The supplier guarantees the timely delivery of products to any address specified by the consumer
Technology of preparatory operations
For cleaning from scale, various etching technologies are used: chemical and electrochemical. For chemical etching, solutions of sulfuric, hydrochloric or orthophosphoric acids are used. The most common etching in sulfuric acid is characterized by a number of disadvantages. The process is environmentally harmful, and the billets after etching in sulfuric acid should be subjected to curing within 24 hours, since after such etching, hydrides of iron are formed on the surface of the steel to increase brittleness. Hydrides are unstable, and eventually decompose completely, but the technological cycle of production in this case is unreasonably prolonged.
The most environmentally friendly is the process of electrochemical etching in solutions of chloride salts. Its drawback is the increased duration of operations.
Sequence of etching — degreasing, washing, etching, washing in hot, and then — in cold water, drying.
For straightening of rolled metal, mechanical presses and rotationally-correct machines are used. The last type of equipment is more productive, since the editing is carried out in a continuous cycle.
Supplier — AvekGlob Company — offers to purchase various metals and alloys, blanks for which are obtained with the help of various cutting technologies. The quantity, accuracy and dimensions of the blanks are determined by the customer’s wishes. Products can be bought at a price formed on the basis of European and world standards of production. Implementation is possible in bulk and retail, for regular customers, a flexible system of discounts operates.