Methods of melting metal
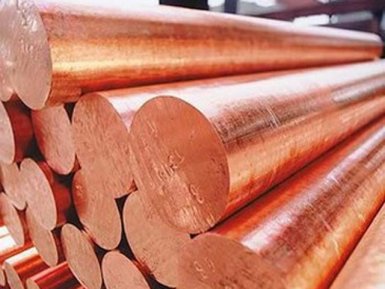
Are you interested in the ways of melting metals and alloys from the supplier company AvecGlob? Here you will find interesting information on this topic /
Principles of obtaining alloys
The vast majority of metals are obtained by metallurgical methods. Alloys are produced by mixing metals in a molten state; then the mixture is poured into metal or sand molds and left to solidify. Typically, the main ingredient first melts; then others are added to it and must completely dissolve.
Some metal pairs do not dissolve in this way. When this is the case, it is unlikely that a useful alloy will be formed. One of the difficulties in making alloys is that metals have different melting points. Thus, copper melts at 1083 ° C, while zinc melts at 419 ° C and boils at 907 ° C. Thus, in the manufacture of brass, if we simply put pieces of copper and zinc in the crucible and heat them above 1083 ° C, both metals will probably melt. But at this high temperature liquid zinc also boils, and the vapor will be oxidized in the air. The method adopted in this case is to first heat the metal with a higher melting point, namely copper. When this is melted, the solid zinc is added and dissolves rapidly in the liquid copper before the zinc boils. Sometimes making alloys is difficult, because a metal with a higher melting point is in a smaller proportion. For example, one light alloy contains 92% aluminum (melting point 660 ° C) with 8% copper (melting point 1083 ° C). In this, as in many other cases, doping is carried out in two stages. First, an intermediate «hardener alloy» containing 50% copper and 50% aluminum is produced, this alloy having a melting point much lower than that of copper and, in fact, lower than that of aluminum. Then the aluminum melts, and the correct amount of hardener alloy is added.
With a careful selection of components, it is possible to produce alloys with unusually low melting points. These alloys with a low melting point are regularly used for more serious purposes, for example, in automatic fire sprinklers installed in building ceilings.
Supplier — AvekGlob Company — offers various metals and alloys at a reasonable price from the manufacturer in a wide range of rolled profiles. The supplier guarantees the timely delivery of products to any address specified by the consumer.
The process of melting metals in the foundry
The melting process begins by determining which type of scrap will be used to load the furnace. At a temperature of about 2000 ° C, the metal is poured into a pre-heated bucket for transfer to the casting line.
On the spill lines, the molten metal is poured into appropriate molds. After pouring, the mold is allowed to cool for about 30 minutes before the sample of the metal is taken for testing. Filled molds are dumped into a vibrating conveyor, where the forms are destroyed by vibration, which provides the casting for removal. Sand from the mold is separated and processed for reuse.
Supplier — AvekGlob Company — offers to purchase various metals and alloys in any quantity and range of profiles. Products can be bought at a price formed on the basis of European and world standards of production. Implementation is possible in bulk and retail, for regular customers, a flexible system of discounts operates.