Welding of copper with brass
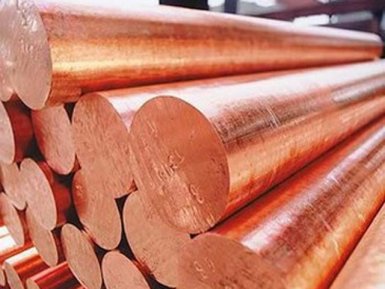
Are you interested in the technology of brass welding with copper from the supplier company AvecGlob? Here you will find the necessary information on this topic.
Weldability of copper and brass
When welding, it is important to understand how to maintain the desired corrosion resistance and mechanical properties, as well as to avoid the appearance of defects in welds. Therefore, the first step to successful copper welding is to familiarize yourself with various copper-containing alloys, their properties and considerations when choosing a filler for each.
Copper is a soft metal in a pure, undoped state. Welding of copper and brass with the use of oxygen is not recommended, since high temperatures cause a significant reduction in the strength and plasticity of the resulting weld. Melting welding is also not recommended, because both copper and brass are very susceptible to cracking. Therefore, high temperatures will overload the zone exposed to heat and reduce its mechanical properties.
With the exception of brass containing lead, all brasses are welded together, and alloys with a low zinc content are most easily welded. Brass with a low zinc content (<20% zinc) has good weldability, whereas high-zinc brass (> 20% zinc) has only limited weldability, and cast brass is almost not welded.
Tin brass alloys have good weldability. Since they are sensitive to hot cracking and tend to form oxide films, copper welding with brass should avoid slow cooling rates. Leaded brass alloys with copper are welded poorly.
Supplier — AvekGlob Company — offers to purchase assortment of various brass alloys of domestic and foreign production. Products can be bought at a price formed on the basis of European and world standards. Implementation is possible in bulk and retail, for regular customers, a flexible system of discounts operates.
Major defects in welding copper and brass
Porosity
Copper and brass are most susceptible to this defect. Therefore, gas welding of the materials in question is not recommended, but instead a filler wire containing deoxidants (Al, Si, Mn, Ti, P) should be used.
Phosphor bronzes are best combined with fillers with a particularly high level of deoxidants, and copper nickel is best combined with fillers containing from 0.2 to 0.5% titanium.
The risk of porosity in brass can be reduced by using silicon or aluminum bronze as a filler. The porosity decreases with an increase in the speed of movement of the electrodes.
Brasses with a low zinc content (<20% zinc) are susceptible to melting defects due to their high thermal conductivity. Consequently, preheating of alloys with a low zinc content before welding is required.
Hot cracking
Copper containing chromium or beryllium alloys is susceptible to this welding defect. The risk of hot cracking can be reduced by using pre-heating before welding. Brasses containing high levels of zinc do not require preheating, but they require slow cooling rates after welding.
Supplier — AvekGlob Company — offers various types of products from brass alloys of domestic and foreign production, which meets the requirements of standards. The products are offered at affordable prices from the manufacturer. The supplier guarantees the timely delivery of products to any address specified by the consumer.