Welding of thin metal
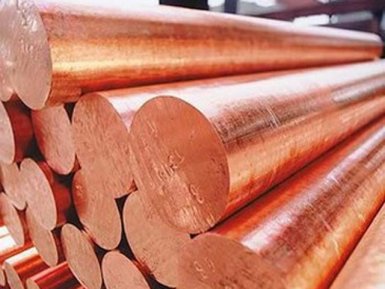
Are you interested in welding thin metal from the supplier company AvecGlob? Here you will find interesting information on this topic /
Variants of application of processes of welding of thin metal
To successfully weld a thin metal, you need to melt some metal, and then lightly cool it until the next batch melts. This avoids the inevitable blowdown of the weld zone, during which the steel can be burned at the drop site of the drop of molten metal.
In order to prevent this, the setting of the welding machine amplifier and wire feed speed should be reduced. Using a thinner wire (0.6 mm instead of 0.8 mm) will also help reduce the operating current of the process.
Welding technique for thin metal
Using MIG technology, welding should be carried out with short impulses, in between which the melt will cool down. The minimum pause between pulses should not be more than 0.5 s, and with increasing pause the chance of getting the influx of cooled metal (which are formed between the seams) increases.
The risks in using this technology are that individual weld beads can not melt with each other, which practically guarantees a reduced strength of the joint. Therefore, this technique is suitable for welding steel sheets at least 0.8 mm. For a thinner metal, TIG is used — welding using a tungsten non-consumable electrode.
Supplier — AvekGlob Company — offers at affordable prices from the manufacturer various metals and alloys, in the quantity and assortment that are required by the customer. The supplier guarantees the timely delivery of products to any address specified by the consumer.
Main features of welding
When welding large sheet panels (for example, a car), thermal expansion of the metal during welding can lead to distortion of the dimensions of the joined products. The problem is that such parts increase in size at high temperatures, so when the shape is correct during welding (when the panel is hot), the product changes shape significantly when cooled.
Distortion can be minimized if the metal is welded at intervals of, for example, 20 mm, and only welding of very short sections (less than 20 mm in length) is performed at a time, allowing the metal to cool between each section of the weld. If the seam is long, then the first section can be on one end of the seam, and the second on the other, and so on.
A good effect is provided by cooling the preforms prepared for welding with a damp cloth between the sections, or by using pads made of a material with a lower thermal conductivity (in particular brass), which are located under the place of the welding seam.
Optimization of the working cycle
Since the duty cycle will be much shorter than with conventional continuous welding in the same welding machine setting, the welder will need longer welding breaks so that the weld metal can cool down.
Supplier — AvekGlob Company — offers to purchase various metals, alloys, welded structures in any quantity and range of sizes. Products can be bought at a price formed on the basis of European and world standards of production. Implementation is possible in bulk and retail, for regular customers, a flexible system of discounts operates.