Welding of thin metal inverter
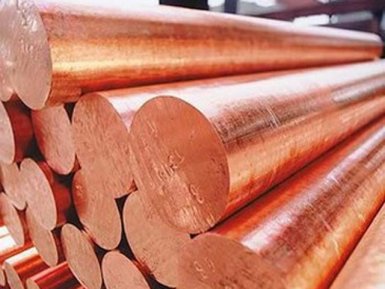
Are you interested in welding thin sheet metal inverter from the supplier company AvecGlob? Here you will find interesting information on this topic /
Advantages and limitations of the process
Arc welding of sheet metal with the use of an inverter makes it possible to get rid of many complications of the MIG welding process, it does not depend much on the qualification of the welder, and also allows to do without costly equipment and consumables (wire, shielding gas cylinders, etc.). In addition, inverter welding machines are mobile enough, cheap and therefore affordable.
Disadvantages of inverter welding when joining thin plates are manifested in the complexity of setting the inverter. In addition, when arc welding generates a lot of heat, which in almost all cases creates thermal distortion of welded products.
Welding Preparation and Conducting
When welding with direct current, its values should not exceed 20… 25 amperes (allowance is made for the duration of the inverter’s inclusion, which for all types of sizes imposes significant restrictions). The arc is ignited at the minimum allowable voltage (short arc) to avoid burnt the sheet. A known practice is required, but if this still happens, it is recommended to have a number of fragments of sheet metal of the same brand next: thus filling the places of burning.
The welding arc is tuned to a direct polarity, with the thermal torch on the electrode, and not on the base metal. By setting the optimum current, the welded / welded parts are pre-positioned in such a way that the lower part of the sheet hangs in the air. The rationale for the last moment is to make it more heavy, and convenient for work.
After igniting the arc, the metal should be moved to maintain a continuous arc. After this, the welder moves to the work area and performs several straight seams. After each weld, remove the slag.
Supplier — AvekGlob Company — offers at affordable prices from the manufacturer various metals and alloys, in the quantity and assortment that are required by the customer. The supplier guarantees the timely delivery of products to any address specified by the consumer.
The formation of joints and the final transitions
The layout of joints on thin sheet metal should be such that it does not allow the arc to deform during welding the ends of the blanks. Therefore, between the parts leave a small gap, and only then start welding, gradually filling the joint with liquid metal. If you try to connect directly, burn is likely. Joints are formed in parts, with a small (50… 80 mm) interval, and then, after cooling the metal in the seams, fill the gaps. Around the joints make ring rollers — this strengthens the thin sheet metal and prevents its burning when the electrode approaches the metal.
The movement of the electrode must be reciprocating. To reduce the heat transfer to the metal, at the end of each cycle the electrode is placed in the bath with the melt, after which it is abruptly removed and continues to be moved in the required direction.
After the end of welding, it is necessary to make corrections before cooling the welded parts, removing the inevitable distortions of the shape of the sheet. To reduce deformation, it is recommended to use metal pads with a larger thickness.
Welding of sheet metal inverter is associated with known difficulties, therefore, sufficient practice is required to perform such work.
Supplier — AvekGlob Company — offers to purchase various metals, alloys, welded structures in any quantity and range of sizes. Products can be bought at a price formed on the basis of European and world standards of production. Implementation is possible in bulk and retail, for regular customers, a flexible system of discounts operates.