Bronze welding with argon
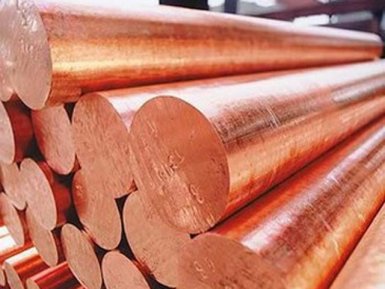
Are you interested in welding bronze with argon from the supplier company AvecGlob? Here you will find the necessary information on this topic.
Features of bronze welding using argon
From the standpoint of weldability, the main problem is that bronzes are sensitive to hot stress cracking, and more phosphorous bronzes are also prone to the formation of oxide films on the weld seam. Therefore, high levels of preheating and slow cooling should be avoided. MIG and TIG welding are the preferred welding processes with argon blends. MIG is more suitable for welding heavier sectional joints, and positional welding is performed with alternating current. For essential components, preheating to 200 ° C is required.
Silicon bronzes are the easiest to weld. They contain between 1.0 and 4.0% silicon with small amounts, less than 1.5%, zinc, manganese and / or iron. Unlike many other copper alloys, the thermal conductivity of such bronzes is relatively low, which allows using high welding speeds and avoiding preheating for thicker joints. The only problem is that silicon tends to form an oxide film on the surface of the weld, which requires vigorous wire cleaning with multiple welding. It is advisable to anneal the components before welding and quickly cool through 1000−850 ° C.
As in the case of other bronzes, MIG or TIG welding using pure argon as shielding gas is used. However, it should be noted that the size of the weld pool should be limited in order to ensure a rapid cooling rate.
Supplier — AvekGlob Company — offers to purchase assortment of various bronze alloys of domestic and foreign brands. Products can be bought at a price formed on the basis of European and world standards. Implementation is possible in bulk and retail, for regular customers, a flexible system of discounts operates.
Argon welding of aluminum bronzes
This family of alloys has in its composition from 3 to 15% of aluminum with additives of iron, manganese and nickel. The characteristic that gives the alloy its corrosion resistance is an aluminum oxide film that forms on the surface. This causes difficulties in welding with argon, so the film must first be removed.
MIG and TIG processes can be used, and in the latter case, the process of heat transfer to the weld is more active. When welding very thick sectional compounds by the MIG process, it is more expedient to use not pure argon, but its mixture with helium.
Aluminum bronzes with an aluminum content of less than 8% are susceptible to hot cracking at temperatures around 700 ° C, and care should be taken to reduce residual stresses as much as possible, ensuring accurate installation and minimum clearances. Procedures with low thermal load should be used, and the temperature of the interval should be up to 150 ° C. These alloys do not require preheating.
Supplier — AvekGlob Company — offers various types of rolled and cast bronze from domestic and foreign production. The products are offered at affordable prices from the manufacturer. The supplier guarantees the timely delivery of products to any address specified by the consumer.