Cutting and making holes in products made of stainless steel
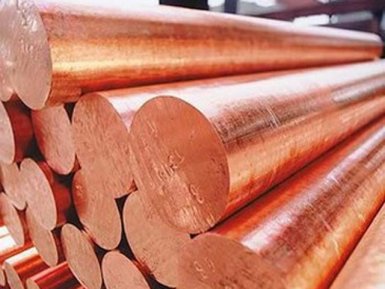
Are you interested in cutting and making holes in stainless steels from the supplier company AvecGlob? Here you will find the necessary information on this topic.
Features of cutting stainless steels
Cutting of blanks from these materials can be performed by mechanical methods or by applications of plastic shearing techniques. For mechanical cutting, band sawing machines, mechanical hacksaws, friction saws, as well as milling and cutting machines are used. In addition, anodic-mechanical and electro-erosive cutting can be used in a single production. Due to the low heat capacity for cutting, plasma arc and laser cutting are not used.
All methods of mechanical cutting are characterized by a large temperature of the tool heating, while the use of lubricating-cooling media is ineffective.
Cutting on scissors and in stamps allows to increase productivity and to avoid the increased wear of the tool. In doing so, try to ensure the minimum value of the working gap between the moving and stationary knives.
The disadvantage of all methods of shearing is the relatively high cost of the working tool and its low universality.
Supplier — AvekGlob Company — offers to purchase assortment of products made of different brands of stainless steels. Products can be bought at a price formed on the basis of European and world standards. Implementation is possible in bulk and retail, for regular customers, a flexible system of discounts operates.
Drilling of stainless steel
The mechanical properties of stainless steels, including heat resistance and high ductility, make them difficult to produce holes. The greatest difference is in the high plasticity of austenitic and duplex stainless steels. These materials also tend to easily harden and form build-up edges on the cutting tool. In particular, in duplex stainless steels, the complexity of chip formation and removal is difficult due to their high strength. When the drill is overheating, it will begin to break down. In drills with high speed of rotation this heat will lead to the fact that the tool loses its hardness. In carbide drills on the cutting edges, microcracks can form, which will eventually lead to the failure of the drill. As the depth of the drilled hole increases, the metal hardens and drilling becomes more complicated.
One way to reduce the effect of hardening the metal is to increase the rear cone of the tool, which reduces the contact area between the tool and the workpiece. In addition to adjusting the angle of the rear cone, other variables in the tool design can facilitate drilling of stainless steels.
The construction of the tool for drilling stainless steel should include:
More precise angle on the cutting edge;
Reduced width of the main sections;
Enlarged rear cone.
In addition, the design of the drilling tool should provide for the constant possibility of its through cooling.
Cooling fluid is necessary both for controlling the drilling process and for extending the life of the tool. The cooling fluid supplied through the tool also helps to evacuate the chips.
Providing sufficient supply of coolant to the cutting area means controlling the pressure. This depends on the ratio of depth to diameter.
Supplier — AvekGlob Company — offers various types of products from stainless steel of domestic and foreign production. The products are offered at affordable prices from the manufacturer. The supplier guarantees the timely delivery of products to any address specified by the consumer.