Roller mills
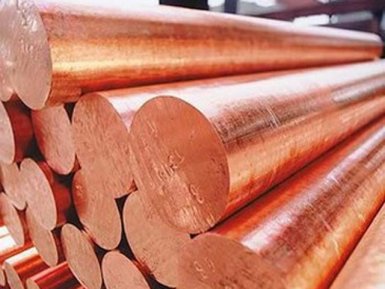
Are you interested in the technology of working on roller machines from the supplier company AvecGlob? Here you will find interesting information on this topic /
Operating principle
Roller machines are designed for forming operations with sheet metal. In most applications, the required cross-sectional profile of the preform is specifically designed to allow the machine to bend the metal as needed. In addition to the production of rolls, these machines perform a number of metalworking operations, including cutting materials and spiraling the metal.
Roller machines often work in a continuous cycle. The material is fed into the machine, where it continuously passes through the stages of each operation, ending with the completion of the final product.
A machine for forming a spatial profile from a flat workpiece bends the metal at room temperature using a number of positions where the fixed rollers guide the metal and perform the necessary bends. When the metal strip passes through the roll forming machine, each set of rollers bends the metal slightly more than the previous roller station. This ensures a correct cross-sectional configuration while maintaining the cross-sectional area of the workpiece.
Urgency of application
Roller machines operate at high roller speeds and are a good choice for the production of a large number of long parts of trays, troughs, spiral pipes that are later to be welded. Machines for forming coils are also used to create precise parts that practically do not require finishing operations. In most cases, depending on the shape of the material, the final product has an excellent surface finish and high precision.
Supplier — AvekGlob company — offers at affordable prices from the manufacturer various models and sizes of roller machines designed for working with sheet metal. The supplier guarantees the timely delivery of products to any address specified by the consumer.
Design
Roller equipment consists of four main blocks:
feed mechanism, where the initial roll or coil with metal is charged;
working rollers / rollers forming the required profile;
guiding knots;
cutting equipment.
All high-performance roll forming machines are equipped with units for unloading finished products.
Benefits
The modern industrial roll equipment is supplied with an automated tool, including CAD / CAM systems, which ensure the optimum roll profile.
In many modern roller machines precision is provided by programmable logic controllers. This is important if part of the workpiece is to have holes, or it must be cut with certain dimensions. Some machines are equipped with welding units.
Supplier — AvekGlob Company — offers to purchase different sizes of roller machines intended for obtaining circular round cross-section blanks from sheet metal. Products can be bought at a price formed on the basis of European and world standards of production. Implementation is possible in bulk and retail, for regular customers, a flexible system of discounts operates.