Tu 48-19-272-83. Molybdenum non-annealed strips. Technical conditions.
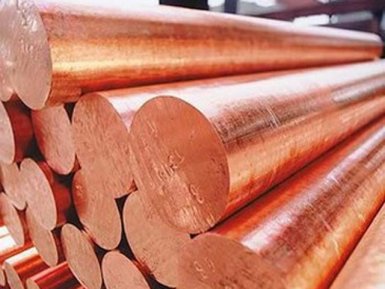
You are interested in TU 48−19−272−83 «Molybdenum strips unburned. Technical specifications «from the supplier company AvecGlob? Here you will find interesting information on this topic.
Application area
These technical specifications apply to unburned strips of molybdenum, which are intended for the manufacture of parts and structures for various purposes, and meet the requirements of the highest and first quality categories.
Technical requirements
Molybdenum bands are made from powder billets of molybdenum grade MCH and ingots obtained by the vacuum melting technology of the MCHVP grade, and by the melting of powdered billets of molybdenum grade MCH.
The initial blanks must be obtained in one of the following ways:
- bands of the MCH brand are made of sintered molybdenum blanks corresponding to the MCH brand (chemically pure molybdenum without alloying additives and impurities);
- the MHP VP grades are made from ingots of vacuum melting obtained from pre-sintered molybdenum packs of MCH grade with the use of carbon as a deoxidizer.
Options for rolling molybdenum bands
Rolling can be done:
- in the cold state — for strips with a thickness of 0.1 to 0.5 mm — in two mutually perpendicular directions;
- in the hot state — for strips with a thickness of 0.6 to 6.0 mm — when rolling in one direction.
Supplier — AvekGlob Company — offers at reasonable prices from the manufacturer a molybdenum strip in the assortment of width and cross section that meets the technical requirements of TU 48−19−272−83. The supplier guarantees the timely delivery of products to any address specified by the consumer.
Nomenclature and chemical composition of molybdenum bands
Depending on the accuracy of the thickness, molybdenum bands of classes 1 and 2 are distinguished. The dimensions of the bands and the tolerances allowed should correspond to the data given in the table:
Thickness | MCH bands | Brand Stamps MCHVP | ||||||
Nominal | Tolerance allowed | |||||||
1 class | Grade 2 | Width | Length | Width | Length | |||
Cold-rolled | ||||||||
From 0.10 to 0.20 after 0.05 | ± 0.02 | ± 0.02 or — 0.04 | from 50 to 250 | from 150 to 700 | from 50 to 250 | from150 up to 800 | ||
From 0.25 to 0.35 after 0.05 | ± 0.02 or ± 0.04 | ± 0.03 or — 0.06 | from 50 to 250 | from 150 to 600 | from 50 to 250 | from150 up to 700 | ||
From 0.40 to 0.5 through 0.05 | ± 0.03 or — 0.06 | ± 0.04 or -0.08 | from 50 to 250 | from 100 to 250 | from 50 to 250 | from100 up to 600 | ||
Hot-rolled | ||||||||
0.6 to 0.6 through 0.1 | - | ± 0.05 or — 0.1 | from 50 to 250 | from 100 to 250 | from 50 to 250 | from 100 up to 250 | ||
From 1.0 to 1.9 through 0.1 | - | ± 0.06 or — 0.12 | from 40 to 150 | from 100 to 250 | from 50 to 200 | from 100 up to 250 | ||
From 2.0 to 3.0 after 0.2 | - | ± 0.1 or — 0.2 | from 30 to 100 | from 80 to 250 | from 50 to 200 | from 100 up to 250 | ||
From 3.25 to 6.0 through 0.25 | - | + 0,12 — 0,13 or — 0,25 | - | - | from 50 to 200 | from 100 up to 250 | ||
The chemical composition of the strips must meet the requirements specified in the table.
Component name | Norm | |
For the brand MCH | For the brand MMHVP | |
Mass fraction of molybdenum,%, not less than | 99.95 | 99,9172 |
Mass fraction of impurities,%, not more than | ||
iron | 0.014 | 0.014 |
aluminum | 0.004 | 0.004 |
nickel | 0.005 | 0.005 |
silicon | 0.012 | 0.014 |
Calcium and magnesium (in total) | 0.005 | 0.005 |
carbon | 0.01 | 0.03 |
oxygen | - | 0.0050 |
hydrogen | - | 0.0008 |
nitrogen | - | 0.005 |
Quality indicators
Strips thicker than 2 mm are supplied without trimming the edges. Strips of 2.0 mm or less should be cut off from all sides. Saws and burrs on the edges are not allowed.
The surface of cold rolled strips should be degreased, hot rolled — cleaned of oxide film. The surface of the strips should be without delaminations, shells, oxides, mechanical damage. Allowed for minor local defects that do not lead to thicknesses beyond the tolerances: dents, roll marks, scratches, pockmarks, scraping traces.
The roughness parameter of the surface of cold-rolled strips according to GOST 2789−73 should be Ra from 2.5 to 1.5. The bands should be even. On strips with a thickness of 0.2 mm or less, the waviness is allowed, disappearing when they are rolled into a cylinder with a diameter of 50−60 mm. Strips 0.5 mm thick and less should be rolled in two directions. The direction of rolling changes by 90 ° after a general deformation of at least 80% from the beginning of the treatment.
Mechanical properties
For cold rolled strips rolled in two directions, they must correspond to the following indices:
Along the rolling direction | ||
Thickness, mm | Ultimate tensile strength, MPa, not less than | Relative elongation,%, not less than |
0.1 | 800 | 1 |
0.2 | 800 | 1 |
0.3 | 900 | 1 |
0.4 | 900 | 1 |
0.5 | 900 | 2 |
Supplier — AvecGlob Company — offers to purchase strips of molybdenum, which meet the requirements of TU 48−19−272−83. Products can be bought at a price formed on the basis of European and world standards of production. Implementation is possible in bulk and retail, for regular customers, a flexible system of discounts operates.