Induction melting of metal
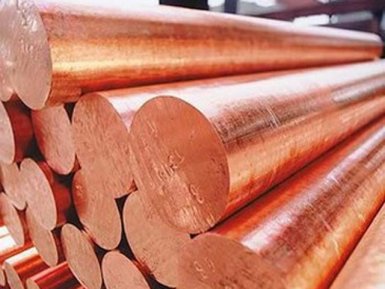
Are you interested in the technology of induction melting of metals from the supplier company AvecGlob? Here you will find interesting information on this topic /
Principle of induction melting
In the process of induction melting, metals and alloys are heated directly in a ceramic crucible, although in some cases it is more expedient to use an intermediate current collector, for example, graphite. Special applications of induction heating allow the melt to levitate, which ensures the smelting of high-purity or highly reactive materials without impurity contamination.
Induction melting can be carried out in a vacuum or in an inert atmosphere (for highly reactive metals). The process of induction melting of a metal can be combined with the possibility of casting to complete the melt and casting within the same system.
Urgency of application
Typical materials for induction melting of metals are copper, gold, silver, most grades of stainless steels, brass, aluminum and other metals. General applications include: remelting of scrap metal of special grades, foundry, smelting of precious metals (gold, silver, platinum), laboratory studies of materials and preparation of samples.
Supplier — AvekGlob Company — offers at affordable prices from the manufacturer various metals and alloys, which are obtained by induction melting technology. The supplier guarantees the timely delivery of products to any address specified by the consumer.
Equipment for induction melting
There are two main types of induction furnaces: channel and heartless.
The basis of an induction furnace without a core is a coil, which consists of a hollow section of a high-strength copper tube with high conductivity, which is wound in a spiral coil. The coil is contained inside the steel sheath, and magnetic shielding is used to prevent the heating of the support shell. To protect it from overheating, the coil is cooled by water, with continuous circulation of water with cooling it in the cooling tower. The shell is supported on trunnions, on which the furnace is heated to facilitate pouring. The crucible is made of refractory material. The frequencies used in induction melting range from 50 per second (network frequency) to 10,000 per second (high frequency). The higher the operating frequency, the greater is the maximum amount of power that can be applied to the furnace of a given power, and the smaller is the value of the induced turbulence.
Such furnaces are used for melting alloys with a high melting point. They are ideal for remelting and alloying due to the high degree of control over the temperature and thermochemistry of the melt,
Channel induction furnaces consist of a refractory lining and a steel tank that contains molten metal.
The induction block consists of an iron core in the form of a ring around which a primary induction coil is wound. This assembly forms a simple transformer in which the loops of the molten metal contain a secondary component. The heat generated in the loop causes the metal to circulate in the main furnace well.
Channel induction furnaces are usually used for melting alloys with a low melting point. They can be used as holders for molten metal with a peak in induction induction inductors without a core, thereby reducing the overall cost of melting and avoiding peak loads.
Supplier — AvekGlob Company — offers to purchase various metals and alloys in any quantity and nomenclature of sizes, obtained by induction melting technology. Products can be bought at a price formed on the basis of European and world standards of production. Implementation is possible in bulk and retail, for regular customers, a flexible system of discounts operates.