Corrosion of the weld for stainless steel
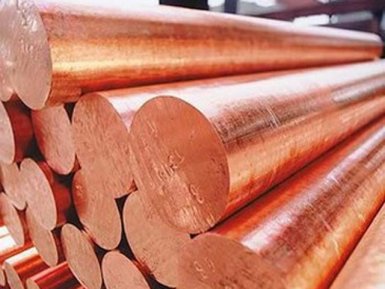
Are you interested in corrosion of the weld for stainless steels, from the company — supplier Alekhlas? Here you will find the necessary information on the topic.
General information
Almost all stainless steels can reduce its corrosion resistance during welding. The effect that the welding process has on the reduction of corrosion resistance, is often ignored.
The spatter, which occurs when the heated areas are not fully protected from oxidation, may indicate a severe loss of corrosion resistance.
Resistance to corrosion is provided by thin but resistant film of chromium oxide which is formed on the surface of stainless steels with a chromium content of more than about 11%. This effect is blocked if the surface layers are changed during the welding operation.
The temperature above which this phenomenon occurs is usually in the region of 400 ° C, which corresponds to a discoloration of the surface. Above this temperature, the color changes to blue and, finally, — to black. To maintain corrosion resistance, coated areas must be removed after welding.
Operations after welding
In some applications it is customary to extend the practice of bleaching and to remove layer after welding, but it takes a lot of time and, when access is limited, it is difficult to achieve success. Some methods require special equipment. Costs after welding, is often ignored, and not considered as part of the welding process. They are largely applied manually and hence subject to significant changes in efficiency. The most effective method of preventing discoloration is the use of technology clean seams.
Supplier — the company Alekhlas — offers to purchase assortimente metal, made of different grades of stainless steels. Products can be purchased at a price formed on the basis of European and world standards. Possible, wholesale and retail, for regular customers a flexible system of discounts.
Ways to reduce corrosion of the weld
Cleaning involves the removal of the oxygen from the heated zones of the weld, displacing the air with inert gas, usually argon. Developed a variety of cleaning methods to meet the requirements to protect the weld from oxidation.
Welding in a stream of inert gas
The air is replaced by incoming inert gas — argon or helium. You should consider the possibility of turbulence and thus capture part of the oxygen in the air. Continuous gas flow can also be costly.
Soluble barriers
They join the surfaces (especially if welded pipe). The result is satisfactory protect, and after welding the discs can be removed by rinsing with water. Should also take into account the thermal resistance of such barriers: they are from welding heat, and water vapor in the presence of a welding arc will break down to form oxygen and hydrogen.
Water soluble film for clean joints
Have the following advantages:
Consist of plastic and does not contain water, which contaminates the weld;
Firmly against the weld seam and can withstand the pressure of purge;
Transparent, so you can monitor the status of the weld.
Monitoring of oxygen content in purge gas
Recommended practice to ensure an acceptable bleaching is to maintain the oxygen level below 50 ppm (0,005%) for stainless steel.
The main characteristics for a suitable instrument are that it must have a sufficient measurement range, and flowing the purge gas within the purge volume.
Supplier — the company Avecho offers various types of stainless steel domestic and foreign production. Products are offered at affordable prices from the manufacturer. Supplier guaranteed timely delivery at any address specified by the consumer.