Manufacture of titanium and titanium alloys
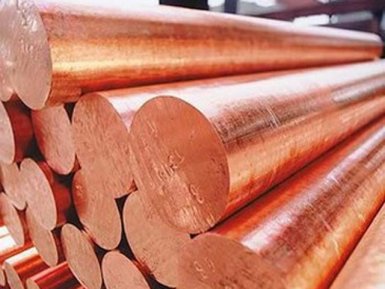
Are you interested in the production of titanium and titanium alloys in the environment of inert gas from the supplier company AvecGlob? Here you will find interesting information on this topic.
Metallurgy of titanium and its alloys
Pure titanium usually has a hexagonal (alpha-α) structure, but when heated above 882 ° C it is transformed into a cubic (beta-β) crystal lattice shape. The addition of alloying elements to titanium affects this transformation temperature and in many alloys, the beta phase is maintained at room temperature, thus obtaining a material containing both alpha and beta phases or even one that is completely composed from the beta phase. The relative amounts of alpha and beta phases in any particular titanium alloy have a significant effect on the properties of this material in terms of tensile strength, ductility, creep properties, weldability and ease of molding.
In the metallurgical industry, it is customary to consider titanium alloys according to their structure, hence, alpha, alpha-beta and beta-alloys. Their production is conducted by two main methods — casting and powder metallurgy
Supplier — AvekGlob company — offers at a reasonable price from the manufacturer various cast or pressed products of titanium and titanium alloys. The supplier guarantees the timely delivery of products to any address specified by the consumer.
Casting of titanium and its alloys
Difficulties in casting titanium due to its inherent characteristics — high reactivity and fluidity of the melt. Conventional methods for the production of titanium and its alloys are not used, since the melt will actively destroy the refractory crucible. Therefore, a technology is used in which a solid layer of titanium is constantly located between the melt and the walls of the crucible. For this purpose, the arc discharge is always directed to the center of the crucible, creating the required temperature gradient. To eliminate harmful impurities in the melt, the crucible is either in a vacuum or in an atmosphere of an inert gas.
Titanium casting requires constant and careful temperature control, as well as monitoring of the gas outlet from the melt zone.
Powder metallurgy of titanium and its alloys
The method is used to produce simple shapes with good dimensional stability, to form shapes with extremely high melting points and to produce titanium parts that can not be produced in other ways. The starting material is titanium scrap, or sponge.
The starting powder is compacted, and the powder itself is obtained by hydrogenation, because this increases the brittleness of the raw material, which contributes to more efficient grinding. The complete removal of hydrogen is economically impracticable, so the powder contains some amount of bound hydrogen. Crushing is carried out in special mills whose abrasive plates are made of titanium alloy. Then the powder is compacted and sintered. Sealing of titanium powders is carried out in the matrix at extremely high pressures, which is created by movable punches. The compact is then sintered in a vacuum oven at temperatures between 1040 and 1100 ° C for one to two hours.
Sintered metal has a slightly lower plasticity than forged or cast product.
Supplier — AvekGlob Company — offers to purchase various designs made of titanium alloys, which are obtained by casting or by methods of powder metallurgy. Products can be bought at a price formed on the basis of European and world standards of production. Implementation is possible in bulk and retail, for regular customers, a flexible system of discounts operates.