Control and finishing of rolled metal products
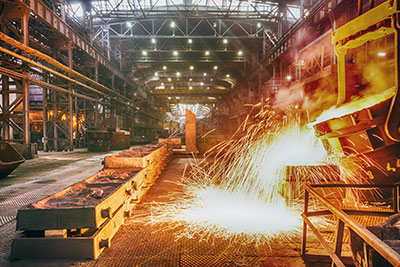
Before you get to the eyes of the immediate consumer, the rolled metal is subjected to control and a variety of finishing operations. Conditionally they can be divided into two categories:
- elimination of surface defects (descaling, stripping, coating);
- improvement of geometric parameters of rolled metal.
Surface defects can be either visible to the naked eye, or can be detected only by special devices.
Rolling control begins at the stage of evaluation of blanks (bloom and slab). According to the principle of technological heredity, the errors in the procurement are transferred to the finished products. In the case of the rolling process, the defects are stretched proportionally to the rolling of the metal. Therefore, a thorough cleaning of the surface is carried out after the first stage of the treatment of rolled products - after blooming or slabbing. According to the practical experience of most enterprises, the elimination of defects in finished products is much more expensive and has an increased labor intensity compared to the cleaning at the stage of the semi-finished product. Therefore, rolling production plans primary finishing operations in the early stages of the overall process.
Control of long products is carried out by inspection and measurement of randomly selected probes. But in the rolling industry, it is very likely that marriage will be allowed in such a valuation method.
One hundred percent objective control of metal rolling should be carried out directly by the flow method, including special control and testing devices in the structure of the rolling mill. Ideally, interconnected individual modules of similar aggregate equipment should be equipped with feedback sensors: if a geometrical inaccuracy of the outgoing rolling is detected, the information signal enters the control system of the rolling mill, adjusting the position of the working organs of the stands.
To detect a defect is small, it should be eliminated without loss of product quality. For long products, the technology of continuous stripping is often used. At the same time, descaling and clarification of the shape of the rolling cross-section are also carried out.
A tool of abrasive and blade type, needle-milling, electric current effect is used. Directly for the cleaning of rolled metal special designs of grinding machines have been developed. For round-section rolling, centreless grinding semi-automatic machines have gained enough popularity, processing a range of sizes ranging from 0.15 to 250 mm in diameter. Flat and shaped rolling is cleaned with equipment using abrasive belts. This method is often used for cleaning high-alloy and high-temperature steels, opening the possibility of local processing.
The most common way to remove scales from metal is still etching in acids. One of the most progressive methods of cleaning is the shot-blasting method: pellets rush to the metal surface at high speeds, removing the surface defect in small parts. Installations of this type are not only highly productive, but also costly, which determines their rare application.
The most important finishing operation of rolling production is the correction - correction of geometric inaccuracy by a consistent stable force action on the rod surface. A special legal equipment for these purposes has been developed, which provides high performance and accuracy at the output.